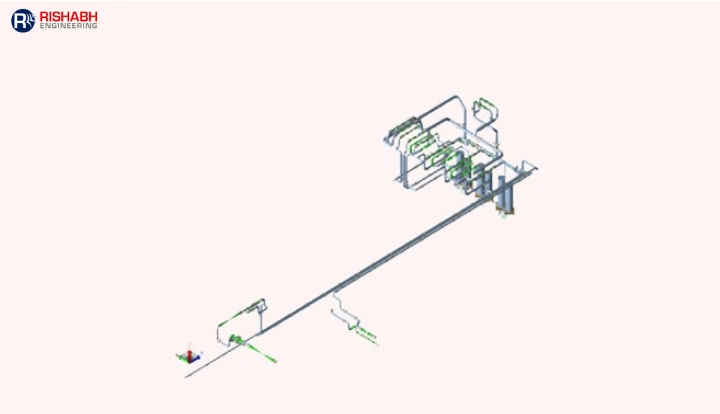
Project Information
Piping Stress And Flexibility Analysis of P79 FPSO Module
Description
Client
A Europe-based Global leader in energy infrastructure, from offshore drilling to engineering solutions.

Engineering Requirement
The client required engineering support for the P79 FPSO piping flexibility and stress analysis project to ensure robust system performance and compliance with industry standards.
Our engineering team managed the entire piping stress and flexibility analysis for the FPSO module, from initial modeling to final report preparation, ensuring thorough analysis and precision. It included stress calculation reports for ~100 systems.
Key activities for FPSO Piping Flexibility and Stress Analysis included:
Piping Layout, 3D Modeling & Detailed Engineering:
- Develop comprehensive piping layouts.
- Create detailed 3D models of the piping systems.
- Perform detailed engineering tasks to ensure system integrity and performance.
Stress and Dynamic Analysis:
- Conduct stress analysis for each system using CAESAR Version 12 Build 200403 software.
- Perform dynamic analyses, including Surge, Slug, Water Hammer, and Vibrations.
- Update CAESAR files with parameters such as geometric design, temperature, pressure, wind, displacement, acceleration, fatigue, and blast pressure.
Computational Fluid Dynamics (CFD) and Finite Element Analysis (FEA):
- Perform CFD simulations to analyze fluid dynamics within the piping systems.
- Conduct FEA for critical components to ensure structural integrity.
Pipe Supports Loads Design, Drawings & Structural Stress Analysis:
- Design pipe supports and calculate load requirements.
- Prepare detailed drawings for pipe supports.
- Conduct structural stress analysis to ensure supports meet necessary standards.
As-built Drawings:
Prepare as-built drawings reflecting the final installed configuration of the piping systems.
Fabrication Drawings and Bill of Material (BOM):
- Create fabrication drawings for all components within the piping scope.
- Develop BOM excluding items covered in the piping scope of supply.
FEA of the Nozzle:
Conduct FEA specifically for nozzles to assess their stress and structural performance.
Deliverables:
Stress Calculation Files:
- Prepare stress calculation files for each system using CAESAR software.
- Include stress analysis cases such as DEC, DOC, DAC, TOW, and BLA (if applicable).
- Generate 5 CAESAR files per system.
Stress Analysis Reports:
- Prepare detailed stress reports for 100 piping systems based on the provided sample report from the client.
- Ensure reports are thorough and comply with all specified requirements.
Final CAESAR Files and AFD Reports:
- Return final CAESAR files to the customer.
- Assist in the preparation of Approved for Design (AFD) reports.
Our piping stress analysis services team ensured the pipe stress and flexibility analysis of P79 FPSO was comprehensive and aligned with client requirements by incorporating geometric design, temperature, pressure, wind, displacement, acceleration, fatigue, and blast pressure parameters.
Want to know more about this project?
Our Recent Projects
Connect with us for all your engineering design needs
US Toll-Free Phone
+1-877-747-4224
India Phone
+91 8511122697
Drop Us An Email
sales@rishabheng.com
Our Offices
USA, UK & India (Head office)