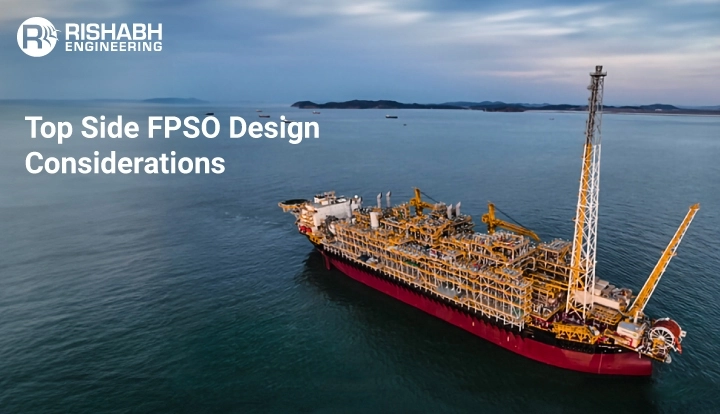
FPSO Topside Module Design With Our Skid Engineering Services
|Floating Production Storage and Offloading (FPSO) units are important offshore oil and gas production components. These adaptable vessels may simultaneously perform production, processing, storage, and offloading activities, allowing for continuous operation in remote areas. FPSO topside design is usually a difficult and multifaceted task. It requires undertaking several essential considerations to assure safety, efficiency, and economic feasibility.
This article will examine the specifics of topside FPSO systems, its various modules, and their role, along with best practices of FPSO Topside Module Design and their real-life use cases.
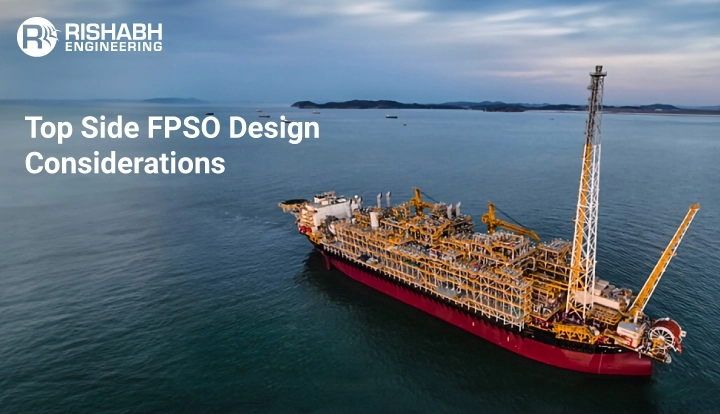
What Does FPSO Mean In Oil And Gas?
Applicable in deepwater offshore oil & gas production, FPSO refers to converted VLCCs (Very Large Crude Carriers), or purpose-built vessels that present a more economical and time-saving solution, depending on world economic conditions.
Purpose Of A Floating Production Storage And Offloading Unit
These process systems separate, store, and transfer oil and gas to shuttle tankers or transportation pipes transporting the commodity onshore.
Did You Know?
Shell was the first company to build what is today recognized as an FPSO. In 1977, the company converted an oil tanker to help with oil production and storage.
Back in the day, oil and gas extraction was limited to shallow waters with floating storage and offloading tankers (FSOs) that were primarily used to store and transport extracted oil and gas to onshore facilities for further processing. The introduction of the Production component in FPSOs revolutionized the industry. These units became invaluable to the oil and gas sector. Process skid manufacturers now play a critical role by engineering, designing, and constructing equipment that separates oil, water, and gas, thereby streamlining the production process.
Read this blog if you wish to unlock the potential of FPSOs in the Oil & Gas industry with specifics on how they work, why they’re useful, the design challenges they face, and how Rishabh Engineering can assist using real-world examples.
FPSO Topside Process Systems
The topside process facility is designed to receive a full well stream from production risers and separate gas, water, and crude oil. Stabilized oil is stored in hull storage tanks, while treated water is discharged overboard. Compressed and treated gas is used for gas reinjection and fuel gas consumption. Seawater is lifted, filtered, and distributed for heat exchange, freshwater production, de-aeration, and sulfate removal for water injection. This separation process ensures efficient and safe operations.
Various Modules And Their Functions
Here’s a breakdown of the varied modules and their respective functions:
- Crude Separation Module: It separates crude oil from water and gas using components like a sand filter, slug catcher, and production separator.
- Crude Stabilization Module: Essential for stabilizing crude oil by removing impurities, it includes an electrostatic coalescer, LP separator, and LLP separator.
- Crude Oil Storage and Offloading System: This system facilitates the storage and offloading of crude oil, featuring an oil cooler and storage tank.
- Water Treatment: Responsible for cleaning produced water to meet environmental regulations, it effectively removes impurities and separates oil.
- Gas Treatment Module: Designed to clean associated gas, this module involves gas compression, dehydration, and impurity removal processes.
- Fuel Gas Treatment: Ensures compliance with air emission regulations by preparing fuel gas for burning.
- H2S Removal: It helps remove hydrogen sulfide (H2S) from gas streams.
- Flare Package: Safely burns off excess gas during emergencies or maintenance procedures.
- Lift Gas Compression: It compresses gas for injection into oil wells.
- Produced Water Treatment Module: Cleans produced water to meet discharge standards, effectively removing oil, solids, and contaminants.
- Heat Medium Module: Manages heat transfer within the system to optimize operational efficiency.
- Desalter Module: Removes salt and impurities from crude oil, ensuring optimum output.
- Separation Module: Efficiently separates gas, oil, and water streams
What Is The Role Of Topside Modules In FPSO Operations?
Listed below are some of the important factors that highlight the important role of topside modules in FPSO operations:
- Production Processing: Topside modules contain equipment for separating, processing, and treating hydrocarbons produced from subsea wells. It is essential for separating oil, gas, and water, ensuring that the extracted hydrocarbons meet quality standards for storage and offloading.
- Safety and Environmental Compliance: Many topside modules are dedicated to safety systems and environmental compliance. They ensure that operations adhere to the safety regulations and environmental standards, thus reducing the risk of accidents, spills, and environmental harm.
- Storage and Offloading: Topside modules include facilities for storing processed crude oil and other hydrocarbons. It allows subsea vessels to accumulate oil over time before offloading it onto tankers for transportation to refineries or other destinations.
- Utility Services: They are critical for maintaining a comfortable and safe working environment for the work personnel and ensuring the smooth operation of production facilities. The services include power generation, water treatment, and HVAC (heating, ventilation, and air conditioning).
- Control and Monitoring: Topside modules typically contain control rooms equipped with instrumentation and monitoring systems for overseeing and managing operations. These systems help monitor equipment performance, control production processes and respond to real-time operational events, ensuring optimal production efficiency and safety.
- Flexibility and Adaptability: Topside modules are often designed to be modular, allowing for flexibility in configuration and easy adaptation to changing production requirements. It enables operators to modify and upgrade facilities as needed to accommodate new reservoirs, production techniques, or regulatory requirements, extending their operational life.
Best Practices For FPSO Topside Module Design
Successful topside design relies on effective decision-making in process optimization, module, piping, electrical, and structural designs. Experienced engineers and designers are crucial in understanding best practices for hull-topside structural interfaces, equipment placement, safety, maintenance, and operability.
Listed below are some of the best practices for your reference. This approach enhances quality, consistency, and efficiency, reducing costs and schedules by minimizing equipment and simplifying fabrication, installation, and commissioning.
- Process Optimization: Optimizing processes before detailed design is crucial for best practices, offering measurable benefits. For instance, an FPSO designed for oil production (100,000 b/d), gas production (250 mmcf/d), produced water (100,000 b/d), and water injection (275,000 b/d at 5000 psig) focused on meeting HSE requirements, maximizing oil export, reducing capital expenses, and minimizing deck space, operating weight, and process complexity. This resulted in an oil stabilization process maximizing recovery and operating at higher pressures, reducing topside weight by 7,000 tons, and saving approximately $300 million.
- Layout: Best practices define living quarters’ locations, safe access/egress, flare, hazardous/non-hazardous systems, and operations for ship loading/unloading, supply vessels, and helicopters. The layout considers mooring methods, sea states, modular process/utility systems, operability, maintenance, and safety. For a spread-moored vessel, flare placement is downwind and far from accommodations. Helicopter approaches align with the wind, avoiding flares, tall structures, and turbine exhaust gases. Supply boat approaches consider met ocean data and dropped-object risks, ensuring safe cargo delivery and unloading. Riser locations opposite the supply boat reduce dropped object risks. Process and utility modules are arranged alongside a central pipe rack, with hazardous modules far from accommodations and utility modules closer. A 20m safe zone separates accommodations from all modules, and laydown areas for short-term storage are exceptions. Equipment is arranged to maintain the FPSO’s center of gravity, with heavy and tall items near the hull centerline.
- Structural: Modular systems simplify shipyard construction, reducing integration costs and schedules. Modules are fabricated, tested, and delivered ready for integration and commissioning. Typically, modules are spaced 1m apart, reduced to 600mm between modules/racks, with a 3m gap from the hull edge for access and egress. Modules adhere to a standard ship length ratio, ensuring support for every tenth of the hull’s length. Pipe racks run along the longitudinal centerline, allowing flexible equipment arrangement. Structural interfaces align with hull bulkheads or frames, and modular support designs account for hull and topside behavior. Sliding stool systems minimize stress on the hull and modules, with pinned stools restricting movement and sliding stools allowing vertical movement. Structures feature lateral bracing at pipe rack changes and racking bracing along lengths. In-place analyses consider operating and extreme conditions, with spectral fatigue analyses for transit and in-place scenarios.
- Piping: Piping design success depends on controlling interconnects between modules, pipe racks, and hulls. Piping on sliding-supported modules should be fixed near the pinned-end, minimizing dynamic stresses. Sufficient offsets enhance flexibility, and piping should route via pipe racks to reduce vessel-induced stress.
- Electrical: FPSO electrical systems benefit from multiple buildings, with main and auxiliary buildings reducing extensive tray routing. Distributed tray runs optimize space, reduce building sizes, and lower module weights. Power generation and large loads are located to minimize high-voltage cabling and voltage drops. Medium- and low-voltage systems are routed to optimize height-to-depth ratios.
Rishabh Engineering Experience with FPSO Design
Listed below are some of the real-life success stories of FPSO design from the Rishabh Engineering team. They helped the clients improve safety, efficiency, and operability while reducing costs and schedules.
Case 1: Laser Scan to 3D Modeling of Topside FPSO Module
Project: FPSO Topside Module Laser Scan To 3D Modeling
Client: A multinational energy corporation specializing in oil and gas managing offshore assets globally.
Objective: The US multinational energy corporation sought a multidisciplinary engineering company’s help for their FPSO gas plant project in West Africa. Rishabh Engineering used laser scans to create a 3D model for the FPSO topside module, covering site survey, data collection, piping, mechanical, civil, structural, electrical, and instrumentation disciplines.
Case 2: Metering Skid Of FPSO Slug Catcher – 3D Modeling & Detailed Engineering
Project: Detailed Engineering & 3D Modeling for Oil & Gas Metering Skid of FPSO Catcher
Client: A specialized engineering contractor in designing, constructing, and commissioning field-proven innovative solutions for Custody Transfer Flow Measurement in the Oil & Gas industry.
Objective: Detail engineering for the FPSO Catcher Oil & Gas Metering Skid included comprehensive shop drawings, 3D modeling in CADWorx, stress analysis, structural calculations, fabrication details, and lifting plans. Deliverables encompassed GA drawings, isometrics, pipe support details, material take-offs, weight and C.O.G. calculations, and final 3D models.
Case 3: Skid Design And Engineering For FPSO Skid Packages
Project: Multi-discipline Detailed Engineering of Compressor Skids, Chiller Skid and Condenser Skid Packages for FPSO Platform
Client: An EPC contractor who provides process cooling, gas compression, natural gas processing, and tank cooling solutions for Oil & Gas and Downstream industries.
Objective: Our team assisted the client with skid package design & engineering for an FPSO platform, ensuring compliance with specifications. Responsibilities included human factors engineering, 3D models for reviews, piping and structural analysis, and various deliverables like GA drawings, stress analysis, and manufacturing drawings.
Final Words
Designing the topside of an FPSO with skid design services involves a complex interplay of structural, process, safety, environmental, and operational considerations. Every aspect must be meticulously planned and implemented to ensure the vessel’s success and lifespan. By addressing on these critical concerns, designers may construct subsea boats that are efficient, productive, safe, and ecologically friendly. As the offshore oil and gas business develops, technology improvements and engineering techniques will improve topside and skid designs, addressing new issues and capitalizing on new opportunities. The ultimate goal remains constant: to create strong, efficient, and long-lasting units that can fulfill modern energy production demands while protecting people and the environment.
Seek Help With FPSO Design?
Our experienced services team can help you with developing comprehensive skid packages by solving complex space optimization challenges & expediting plant upgrades globally.
Related Blogs
Related Blogs
Modular Process Skid Packages – Types and Benefits
Modular Process Skid Packages are today emerging as the most…
Critical Considerations For Choosing The Right Modular Skids
Modular Process Skid Packages, commonly called modular skids, are compact,…