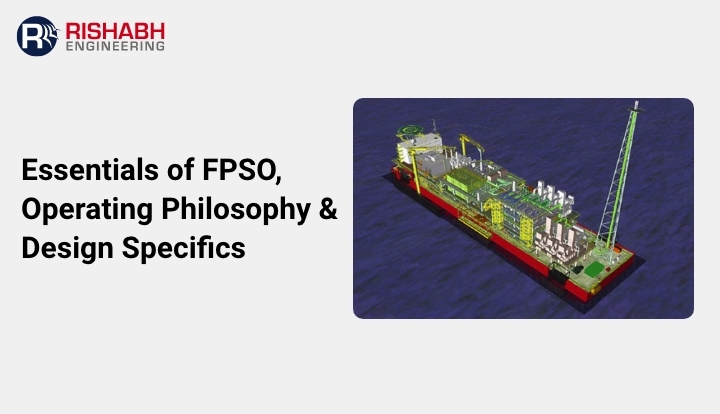
Unlocking the Potential of FPSO in Oil & Gas
|The offshore production of hydrocarbons is moving into deeper and more remote locations. FPSOs (Floating Production, Storage, and Offloading vessels) are proving essential for cost-effective oil production, storage, and offloading. They operate as floating factories outfitted with tools, thus supporting the processing of crude oil and gas from underwater wells while ensuring safety and compliance with standards. They are vital components of the offshore oil and gas sector.
In this piece, we’ll look at the function of FPSOs in oil and gas: how they work, why they’re useful, the design challenges they face, and how Rishabh Engineering can assist using real-world examples.
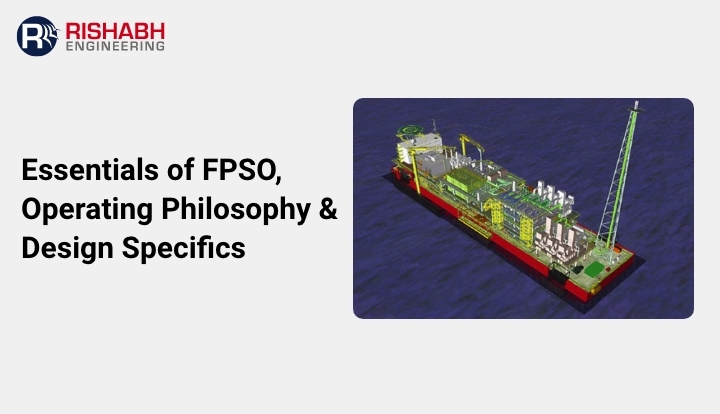
What is an FPSO?
FPSOs are sea-based floating vessels for oil production, storage, and offloading. They permit the processing and storage of oil and gas. FPSOs are widely utilized in the offshore industry as a principal oil and gas production, processing, and storage technique. Oil and gas corporations typically lease them. The boats contain diverse processing equipment that aids in the separation, storage, and offloading of crude oil and gas collected from subsea oil wells or platforms. After processing the oil and gas, FPSOs store it safely before offloading it into a tanker or transporting it via pipeline.
How Does An FPSO Work?
FPSOs are meant to gather hydrocarbons produced by themselves or from nearby platforms or subsea templates, process them, and store oil until it can be offloaded onto a tanker or, less commonly, supplied via a pipeline. They are suited for a wide range of water depths and environmental conditions and can be constructed to operate for at least 20 years.
FPSOs are used in the following situations:
- Marginal fields: Fields with a reserve of 15 to 20 years
- Remote wells: Wells that are far from onshore facilities.
- High-cost onshore facilities: While constructing onshore facilities is expensive, FPSOs are cost-effective units since operators move into deeper waters.
FPSO Components
The main parts of FPSO include:
- Hull: It is the top of the ship above sea level, and it is either newly built or made from the conversion of existing tankers. Often, hulls are designed to match project-specific conditions, which can vary greatly depending on the regions in which it will operate.
- Mooring System: This equipment ensures that the FPSO safely stays in place despite whatever natural forces, waves, winds, and currents it faces. It comprises of mooring lines, anchors, and connectors.
- Topside: It is the gas processing unit for the FPSO at the top of the vessel, and it is designed & constructed for specific offshore platforms while adhering to refinery standard specifications (API & ASME).
- Risers: This component allows the vessel to move vertically and laterally. The flexible steel reinforced risers are designed to absorb any motion that affects the vessel’s position by waves.
- FPSO Turret: It is an integrated part of the FPSO hull. It helps the hull weathervane around the mooring system and the mooring line, allowing the FPSO to rotate freely while mooring to different seafloor locations. This is especially true for adverse weather conditions on the vessel. Furthermore, detachable turret systems allow the turret to be detached from the vessel while remaining linked to the seabed’s mooring lines. This is especially effective in situations like hurricanes and storms, where the vessel must respond swiftly to external risks.
- Gas, water, and oil separator: Water, gas, and oil have different densities, which implies that they can be split in a special separator. And, with gas rising to the top, water on the bottom, and oil staying in the middle.
Types of FPSO
FPSOs are classified into four types based on their processing & storage capabilities, as listed below;
- Floating, Storage, and Offloading (FSO) unit
- Floating, Drilling, Production, Storage, and Offloading (FDPSO) unit
- Floating, Production, Storage, and Offloading (FPSO) unit
- Floating, Storage, and Regasification Unit (FSRU)
Advantages of FPSO
- Cost-effective: FPSOs are less expensive than typical offshore oil and gas installations and offer more flexible leasing arrangements.
- Flexible: FPSOs can connect to any pipeline and be relocated if an oilfield is depleted. This saves time and money by removing the need to construct costly permanent pipelines and infrastructure.
- Safe: FPSOs are safer than conventional methods. They can also be unplugged from the pipelines and oil wells attached to them.
- Timesaving: FPSOs can be extremely effective in deep ocean and remote regions where seabed pipelines are not viable.
- Environmental considerations: Regarding environmental concerns, FPSOs provide major advantages.
Disadvantages of FPSO
- Construction time: FPSOs take around 1-2 years to build or convert and require a costly and timely environmental study for a specific field once accepted.
- Maintenance: FPSOs require careful maintenance and inspection to ensure their optimal performance.
Engineering Design Process To Develop FPSO Packages
Detailed engineering design is a multifaceted process that involves various disciplines working in close collaboration. During this phase, the conceptual designs are refined and converted into executable plans.
Below is the list of activities for designing FPSO packages;
1. Conceptual Design: We start by specifying the FPSO’s basic parameters by creating preliminary sketches and layouts. It would specify the vessel’s dimensions, capacity, and operational requirements. The type of oil or gas to be processed, estimated production rates, and environmental conditions at the offshore location are all important concerns.
2. Front-End Engineering Design (FEED): FEED bridges the gap between conceptual design and detailed engineering by conducting in-depth analysis to refine the design concepts. It would usually involve the selection of key equipment for process flow diagrams (PFDs) and further designing pipe and instrumentation diagrams (P&IDs). Furthermore, this process also outlines the cost estimates and risk evaluations to ensure the project’s viability.
3. Detailed Engineering: This phase involves designing the component by considering all the technical specifications. This design phase encompasses several key activities:
- Process: Detailed calculations are performed to size the equipment and pipelines. This would include thermal, hydraulic, and mechanical calculations, ensuring the system operates efficiently under all expected conditions.
- Mechanical: This would include mechanical components, including pressure vessels, heat exchangers, and rotating equipment, which are designed in detail. This involves specifying materials, dimensions, and construction methods.
- Structural: Structural integrity is critical for its safety and longevity, enabling engineers to design the hull and topside structures, considering factors such as weight distribution, stability, and resistance to environmental loads like wind, waves, and currents.
- Electrical and Instrumentation: This process comprises developing the electrical power distribution system, control systems, and monitoring and control instruments. It starts with generating thorough wiring diagrams, loop diagrams, and control logic.
- Piping: They are important in transporting fluids between process units. Intricate piping layouts, isometrics, and support designs are methodically created to ensure safe and efficient fluid flow.
- Safety and Environmental: A comprehensive engineering design firm conducts hazard analysis, safety studies, and environmental impact assessments to identify potential risks and develop mitigation methods. This includes creating safety measures such as fire detection, suppression, and emergency shutdown of systems.
4. Procurement and Construction: During this phase, all required materials and equipment are purchased. Following that, the FPSO could be assembled either at a shipyard or using modular building methods. Furthermore, the modules are hauled to the offshore site and assembled for the final construction. An experienced multidisciplinary design engineering company is equipped to assist you with vendor evaluation & selection as per the project requirements.
5. Commissioning and Start-Up: After construction, the FPSO undergoes commissioning, where all systems are tested to ensure they function as intended. It would usually include functional testing, performance verification, and safety checks. And, once the floating platform achieves All OK, it is ready for start-up and can commence production operations.
While FPSOs are required for deep and ultra-deepwater operations, collaborating with the proper design firm is critical to the success of your complicated FPSO projects. A knowledgeable design partner can assist you in developing a variety of bespoke packages specific to your FPSO requirements. However, selecting the ideal partner for your project necessitates considerable analysis. To make an informed decision, you should consider these key factors for selecting the best design partner for your FPSO packages.
What Are The Potential Design Challenges With FPSO?
Floating production storage and offloading (FPSO) installations have several design challenges, including:
- Environmental impact: FPSOs are designed to achieve net-zero environmental impact. However, conventional methods, such as gas turbines to generate electricity, can create emissions, and venting can release harmful gases.
- Space availability: This being a floating platform, every space available needs to be utilized optimally, still managing operation and maintenance ease.
- Demolition of existing process modules: Demolition of existing modules as needed based on the type of field and technology enhancement becomes very challenging.
- Installation and integration of new modules: Installation of new modules on the FPSO while at sea is very challenging as it involves careful design and activity sequencing.
- Technical challenges: FPSOs operate in harsh offshore environments and must meet strict safety and environmental regulations. Poorly designed compressors can cause unstable operation, low efficiency, and recycle valve freezing.
- Lack of standardization: Different FPSO projects may not be standardized, leading to challenges.
- Stakeholder management: FPSO projects usually involve multiple stakeholders, including project owners, engineering firms, construction contractors, and regulatory bodies.
- Budget and schedule risks: The time spent in the shipyard is dictated by how well the FPSO aligns with the next field’s requirements. For example, if the new field has an anticipated life of 20 years, but the FPSO has a remaining structural fatigue lifespan of 10 years, that’ll be an issue.
- Refurbishment: Refurbishment is required to enhance the working life of FPSO by extensive repair and modernizing existing process equipment. Integrating new technology into the existing one requires As-Built data, which is often missing.
How Can The Rishabh Engineering Team Help?
Our team assists with FPSO design while addressing the challenges through their experience in engineering and design services. It involves using various standards, codes of practice, specifications, and national and international laws. FPSOs are designed and built according to sea conditions, production period, production volume, and installation requirements.
Here are some ways how our team can help;
- Structural Engineering: Structural engineers play a crucial role in designing the topsides of the FPSO while ensuring that the structure survives various environmental loads such as waves, wind, and currents. To ensure FPSO’s longer operational lifespan, our engineers’ consider factors like fatigue, corrosion, and structural integrity.
- Skid Engineering: We have vast experience conceptualizing and designing process modules/ modular skids to help address space and integration challenges.
- As-Built data capture: Our team can help capture As-Built data using Laser scan.
- Mechanical Engineering: Mechanical engineers design the machinery and equipment onboard the FPSO, including pumps, compressors, turbines, and mooring systems, while ensuring reliability, efficiency, and safety in the operation of FPSOs.
- Process Engineering: Process engineers optimize equipment and piping systems layout while designing the production and processing facilities on the FPSO to separate oil, gas, and water efficiently. This is while meeting production targets and adhering to safety and environmental regulations.
- Electrical Engineering: The electrical engineers design the electrical systems onboard the FPSO, including power generation, distribution, and control systems, thus ensuring a reliable power supply for related equipment & systems, and adhering to safety measures such as grounding and lightning protection.
- Instrumentation and Control Engineering: Instrumentation and control engineers design the automation and control systems to monitor and regulate various processes onboard the FPSO while implementing safety shutdown systems, control valves, and instrumentation to ensure safe and efficient operations.
- Safety Engineering: Safety engineers work to identify and mitigate potential hazards onboard the FPSO while conducting risk assessments, implementing safety procedures, and designing safety features to protect personnel and the environment.
Softwares We Utilize In The Design Engineering Of FPSO Packages
Below are some of the key softwares that the designers & engineers at Rishabh Engineering commonly utilize for developing FPSO Skid packages:
- Process Simulation: This software, such as Aspen HYSYS, Aspen Plus, and others, would allow engineers to simulate various operating situations to conduct sensitivity analysis and enhance design performance and safety.
- 3D Modeling and Design: The models are created using software like AutoCAD Plant 3D, AVEVA E3D, and Bentley MicroStation. They provide a visual representation of the design and facilitate clash detection and design reviews. It would create structures, including the hull, topside modules, piping systems, and structural components.
- Finite Element Analysis (FEA): Structural analysis during the design of FPSO components ensures that the vessel can withstand extreme scenarios in an offshore environment. It enables identifying potential weaknesses while ensuring that the design meets safety & performance criteria with software such as ANSYS and more.
- Piping: It requires precise calculations and layouts, allowing the designers & engineers to create detailed piping isometrics and perform stress analysis, thus ensuring compliance with industry standards. It is achieved using software such as Hexagon SmartPlant 3D and Bentley AutoPIPE.
- Electrical and Instrumentation: It is facilitated by specialized software such as ETAP and more, enabling engineers & designers to develop power distribution systems, control systems, and safety instrumentation, thus ensuring they operate reliably and safely.
- Project Management: It is essential to coordinate various project activities with Microsoft Projects that are commonly used to create schedules, track progress, and manage resources. These tools help ensure that the project stays on track and within budget.
Real Life Use Cases
Case 1: Metering Skid of FPSO Slug Catcher
Project: Detailed Engineering & 3D Modeling for Oil & Gas Metering Skid of FPSO Catcher
Client: Metering Skids Supplier
Objective: Rishabh Engineering executed detailed engineering for an Oil & Gas Metering Skid of FPSO Catcher, integrating CADWorx for a comprehensive 3D model. Our scope encompassed GA drawings, pipe stress analysis, structural steel calculations, piping, and structural fabrication drawings, and MTOs for all elements, including weight, COG, lifting, and monorail calculations, delivering a fully optimized solution meeting client specifications and regulatory standards.
Case 2: Laser Scan to 3D Modeling of Topside FPSO Module
Project: FPSO Topside Module Laser Scan To 3D Modeling
Client: A multinational energy corporation
Objective: Rishabh Engineering undertook a crucial project for a leading US-based multinational energy corporation, aiming to revolutionize the FPSO gas plant project in West Africa. By leveraging advanced laser scanning techniques, our multidisciplinary team helped with Laser Scan to 3D Modeling of the Topside FPSO Module by meticulously executing site surveys, collecting data, and generating dynamic 3D models across various disciplines, including piping, mechanical, civil, structural, electrical, and instrumentation. This comprehensive approach facilitated precise layout design, equipment positioning, and detailed reports, ensuring optimal functionality and efficiency for the FPSO topside module.
Final Words
FPSO is essential in offshore oil & gas extraction as it offers flexibility, cost-effectiveness, and safety. They are important in oil & gas production while contributing significantly to the industry’s sustainability. As a multidisciplinary engineering services company, we at Rishabh Engineering are witnessing a global resurgence in FPSO projects in regions including West Africa, the Middle East, and Latin America. We are working with leading O&G companies & operators to support their FPSO development while ensuring safe and efficient production.
Seek Help with FPSO Design?
We can help design your FPSO modules to optimize performance to enable you to drive offshore oil & gas efficiency and sustainability.
Related Blogs
Related Blogs
Detailed Engineering Considerations for Project Success
Engineering projects today require meticulous planning and execution across various…
Navigating the Green Hydrogen Value Chain
Green hydrogen is a powerful contender for a more sustainable…