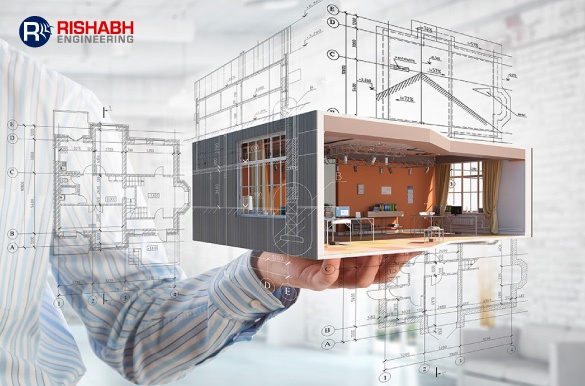
3D Model Review Checklist In Process Industries
|3D models have revolutionized how process industries plan, construct, and maintain their facilities, from designing complex industrial plants to visualizing intricate equipment layouts. Therefore, in today’s dynamic process industries, 3D modeling technology helps achieve the right precision & efficiency. However, with the growing complexity of projects & the involvement of multiple stakeholders, ensuring accurate and effective 3D model reviews has become essential.
This blog will present a comprehensive guideline for conducting 3D model reviews across process industries. It is aimed at optimizing project outcomes & streamlining collaboration among teams. And by following the said best practices, organizations can enhance their overall productivity, minimize errors, and deliver projects successfully within budget & schedule constraints.
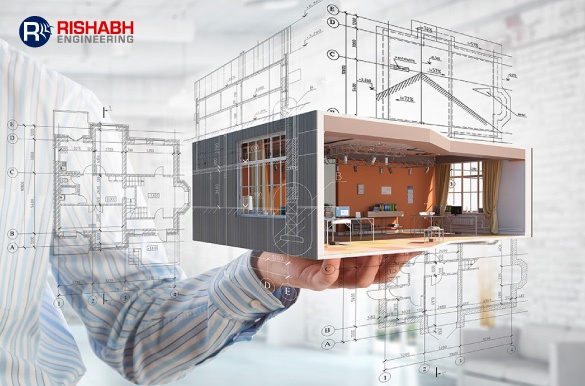
What is a 3D Model & What is the Purpose of Pre-Designing?
A 3D model refers to a collection of graphical data that describes the facilities of a plant for visualization purposes. It helps to portray real-world and conceptual visuals in a simulation through drafting software to navigate the accurate interpretation of drawing and the physical look and positioning of some plant components. Further, it can be accessed via various visualization applications. The graphical data are an integral part of an engineering database supporting the design process with specialized 3D CAD modeling services.
What is a 3D Model Review?
A 3D model review refers to the process of the evaluation & analysis of a digital representation to assess accuracy, quality, and adherence to the suggested specifications. As part of the process, feedback helps identify errors & improve the model before finalization while ensuring optimal performance & alignment with intended objectives.
Pre-designing Purpose:
A plant is first drafted in a 3D model and pre-designed to fulfill the following purpose:
- To select a preferred and more efficient alternative for the project
- For development and set of project goals
- Develop design criteria according to the requirements
- Looking for some alternative analysis
- To identify potential hazards and risks
- For developing a conceptual plan with cost estimation
- Identify stakeholders and make individuals responsible for some specific work
- To recognize the required regulatory compliance
- For determining NEPA/SEPA guidelines
Advantage:
Utilizing a 3D CAD engineering database offers several benefits, including ensuring document consistency and enhancing coordination among various disciplines. It seamlessly integrates different engineering phases, such as piping, foundations, structures, equipment, electrical, and instrumentation, into a single CAD model, free from clashes or conflicts.
Design Criteria Aspects
The CAD project should be structured in a way that all disciplines meet engineering criteria w.r.t.:
- Safety
- Operability
- Ergonomics
- Constructability
- Accessibility for Maintenance & Fire Fighting (valves location, construction convenience, instrumentation, proper routing of piping, location of firefighting equipment, safe & adequate location for vents & drains & escape routes).
3D Model Review Stages
Listed below are key considerations across 30, 60 & 90 percent design review phases.
30 Percent Model Review
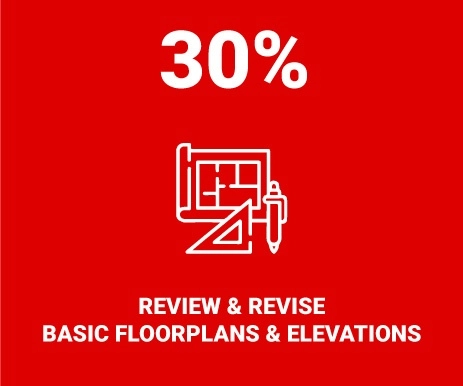
Should include:
- Location of all mechanical equipment
- Maintenance reserved areas (tube bundle pulling laydown areas, access with cranes, forklift trucks, hydraulic working platforms)
- Critical process lines & major piping routing, including control valves, relief valves & supports
- Major inline instruments
- Main Utility lines
- Equipment Spacing Criteria
- Pipe racks, steel & concrete structures (identifying piping access requirements including stairs, ladders, preliminary gratings & major piping supports
- Battery limit Concept (valving, spade/ spacer)
- Outlining of buildings (control rooms, analyzers, switch rooms)
- Defining main E&I cable routes, UG piping & trenches, roads, paving & curbed areas
Objectives:
- Agreement with the client on equipment & plant layout, finalization of equipment location, dimensions & locations of pipe racks, structures & buildings
- Release of foundation loads
- Release of nozzle orientation information to vendor
- Release of main underground isometrics for fabrication
60 Percent Model Review
Should include:
- Resolution of 30% model review comments
- > / = 6″ piping details
- • Equipment & machinery as per vendor information (including orientation of process, instrument nozzles, platform & ladders)
- Level control instruments & other instrumentation on equipments
- Process & Utility lines (= / > 3″ NPS) including supports, flow measurements & main instrumentation
- Permanent cranes & hoisting beams
- Representation of major platforms for equipment & valve operations
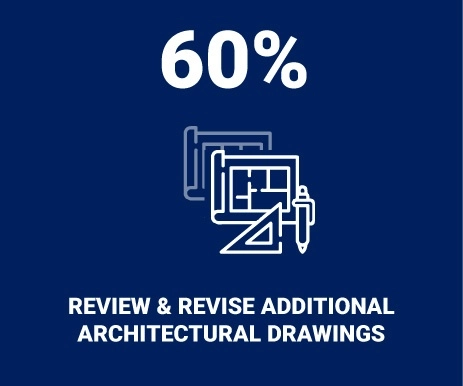
- Electrical & Instrumentation raceway envelopes located on racks & other areas
- Location of pits & trenches
- AG major cable trays
- Remote mounted instruments
- Lighting posts
Objectives:
- Member sizing
- Release of UG Isometrics for IFC
- Release of final nozzle orientation information to vendor
90 Percent Model Review
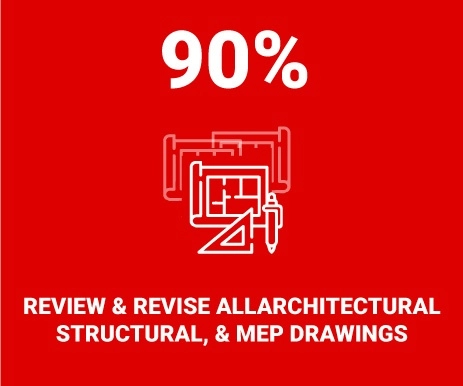
Should include:
- Resolution of 60% of model review comments
- 90% of all lines modeled with all supports, inline items, drains, and vents; except minor small bore & utility lines
- Location of Utility stations w/o final routing
- Availability of all minor and major steel & concrete structures
- Junction boxes & UG cable trays
Objectives:
- Release of UG Isometrics for IFC
Basis of review:
- Detailed agenda including schedule, checking features (for equipment, Structural Steel and Civil, Pipe Stress Analysis and Pipe Supports, Safety, Piping) & systems description meant for review should be issued before 90% model review.
- Marked-up latest P&IDs & pre-defined systems as per latest P&IDs. All lines in P&IDs should be allocated in following different categories:
– Marked-up yellow………(detailed review)
– Marked-up green……….(detailed review but spot checks only)
– Marked-up red…………..(no review only minor process/ utility lines)
– Marked-up pink………..(no review lines within vendor supplied package unit)
Source Reference – https://www.linkedin.com/pulse/3d-model-review-guideline-process-industries-sanjay-sengupta/
3D Model Review Checklist
The checklist w.r.t. the following will eventually help to improve quality, identifying & eliminating potential hazardous situations:
- General Safety, Operability & Maintainability
- Fire Prevention & Safety Equipment
- Piping, Valves, Heat Exchangers, Compressors, Pumps, Vessels, Columns
- Relief Systems
- Packages
Marked-up p&ids and agenda for 30/60/90% design reviews must be prepared & submitted by the detail engineering contractor to the client before the 30/60/90% design review
Model Review Participants
According to the 3D model review procedure, the contractor is responsible for informing the client & all relevant disciplines regarding the venue and schedule of model review sessions. The following participants are expected to attend each model review session:
Client Representatives
- Process: Full-time involvement
- Maintenance: Full time
- Construction: Full time
- Operations: Full time
- Project Engineers: Full time
- Other Discipline: Full-time/As per requirement
Contractor Representatives
- Project Manager/ Engineers: Full time
- Model Drafting Team: Full time
- Lead Piping engineer: Full time
- Process engineer: Full-time for process-related clarification
- Mechanical Engineer
- Instrument/Electrical engineer
- Structural Engineer
- Safety engineer: Full time
- HVAC: As per requirement
- Civil Engineer: On call
Responsibilities in Model Review
3D model review should be organized by the contractor. Here’s a list of responsibilities to be carried out for a successful model review meeting.
Work Activity | Responsibility |
Review Schedular | Project Manager |
Document preparation | Project Engineer |
Review document distribution and agenda sharing | Project manager/Project engineer |
Venue finalization for model review | Project engineer |
Tool Review and creation of model file | Design Administrator |
3D CAD model – Report status | Lead piping engineers |
Hold item list reporting | Lead piping engineers |
Summary & action list preparation | Project engineer |
Action list report – Review, reconciliation & distribution | Project manager |
Action list – Follow up & Updation | Project engineer/Lead piping engineer |
Review model and Status files | Design administrator |
Final Words
It is rare for a design to be finalized in a single iteration, as there are typically review comments and the need to incorporate new updates. To address this, a systematic approach known as the 30-60-90 model review system has been implemented. This process allows for iterative design review and refinement at specific milestones, specifically at 30%, 60%, and 90% completion stages.
System Benefits:
The implemented system provides guidance in several key areas, including:
- Clearly defining the requirements and objectives for each model review milestone
- Establishing specific design requirements for each discipline, such as mechanical, civil, piping, electrical, and instrumentation
- Ensuring that design requirements are updated based on review feedback and guidelines
- Outlining the necessary supporting documents required for model review meetings
- Defining the roles and responsibilities of individuals involved during model review sessions
Seek help with 3D Model Review?
Our experienced team can help you to optimize designs, resolve clashes, and enhance collaboration while ensuring a seamless and successful project.
Related Blogs
Related Blogs
Plant Reverse Engineering Services
What is Reverse Engineering? An engineering process implemented for enhancing…
Best 3D Plant Design Softwares for Multi-Disciplinary Engineering
In the modern context, the modeling and analysis of new-age…