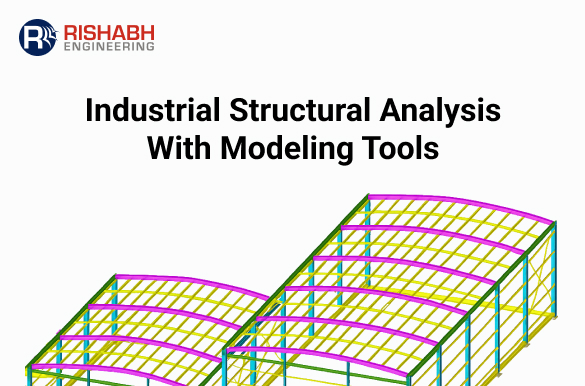
Understanding Structural Analysis Types and Tools
|A key component of engineering that guarantees the performance, stability, and safety of structures under varied loads and circumstances is structural analysis. Buildings, bridges, industrial platforms, and equipment support systems are among the structures whose responses to applied stresses, environmental factors, and dynamic impacts are evaluated. Selecting the best approach depending on the complexity of the project, the behavior of the materials, and the design specifications requires an understanding of the many forms of structural analysis. These kinds range from straightforward static analyses for calculations involving loads to sophisticated dynamic and nonlinear analyses employed in complicated or high-risk engineering settings. Engineers now use advanced tools and simulation approaches to more accurately replicate real-world conditions thanks to technological breakthroughs, resulting in more dependable and effective designs.
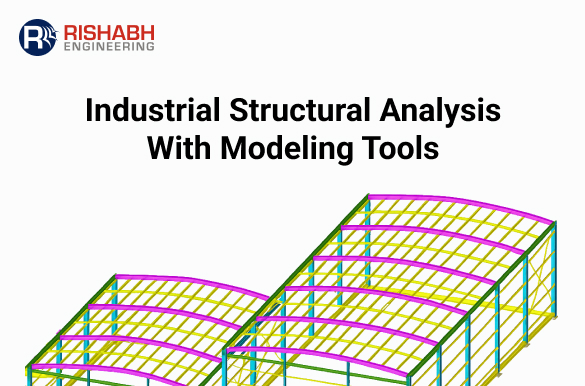
This blog explores the key types of structural analysis, role of advanced software tools, along with Rishabh Engineering’s approach to industrial structural analysis in modern engineering design across diverse industries.
Why is Structural Analysis Critical to Engineering Success?
From large infrastructure to compact industrial equipment, structural analysis is a non-negotiable element of modern engineering. It allows designers to:
- Predict failure points before they occur
- Optimize materials and design for cost-efficiency
- Ensure compliance with safety codes and standards
- Extend the life and usability of structures
- Minimize downtime, damage, and operational risk
Read this blog to learn more about structural analysis & design, why it is performed, its requirements.
Types Of Structural Analysis
Engineering specialists can forecast and guarantee the safety, strength, and stability of different structures thanks to structural analysis, which is a fundamental process. For engineering projects to be viable and operate efficiently over the long term, structural integrity is essential for everything from buildings and bridges to skids and process equipment. Structures are exposed to a variety of loads and environmental factors, making precise and sophisticated analysis essential. There are several varieties of structural analysis, all of which are designed to evaluate various facets of a structure’s performance under circumstances. Static forces, dynamic interactions, thermal loads, fatigue from repeated usage, and the possibility of buckling under compressive stress are just a few of the real-world obstacles that these studies help designers overcome when developing components.
1. Static Structural Analysis
Definition and Purpose:
Static structural analysis is the most fundamental type of structural analysis technique. It assesses the response of structures under steady-state loading conditions—meaning the applied loads do not change over time. These include dead loads (self-weight of the structure), live loads (occupancy loads), and environmental loads such as snow or wind considered in a steady form.
Key Factors Evaluated:
- Displacements
- Internal forces and moments
- Stresses and strains
- Reaction forces at supports
Why It Matters:
This form of analysis is widely used in civil, mechanical, and structural design. It’s crucial in determining the strength and deflection of beams, columns, frames, and supports.
2. Dynamic Structural Analysis
Definition and Purpose:
This type of analysis goes a step further by incorporating time-varying or inertial forces. It examines how structures respond to loads that vary with time—like machinery vibrations, seismic activity, wind gusts, or impacts. Unlike static analysis, it accounts for mass and damping properties.
Types of Dynamic Loads:
- Harmonic loads (vibrations from rotating equipment)
- Impulse loads (sudden impact forces)
- Seismic loads (earthquakes)
- Transient loads (non-repeating, time-varying loads)
Approaches:
- Modal Analysis: Determines natural frequencies and mode shapes.
- Time-History Analysis: Simulates structure’s response over time.
- Response Spectrum Analysis: Evaluates seismic response using a spectrum curve.
Why It Matters:
Dynamic analysis is critical for equipment foundations, tall structures, and mechanical components that encounter time-varying forces. Failing to account for resonance or natural frequencies can lead to catastrophic failure.
3. Finite Element Analysis (FEA)
Definition and Purpose:
Finite Element Analysis is a numerical simulation method used to predict how complex structures behave under various physical effects. The structure is divided into a mesh of smaller finite elements. Equations are solved over each element to determine stress, strain, and deformation across the structure.
What It Evaluates:
- Non-linear behavior (material and geometric)
- Complex load combinations
- Temperature-induced stress
- Localized stress concentrations
- Detailed failure prediction
Benefits of FEA:
- High precision for irregular geometries
- Visualization of stress hotspots
- Optimization of component thickness and material
Use Cases:
- Heat exchangers
- Pressure vessels
- Skid-mounted equipment
- Offshore and marine components
- Mechanical joints and baseplates
4. Fatigue Analysis
Definition and Purpose:
This analysis evaluates the effects of repeated cyclic loading, which can lead to microscopic crack initiation and, ultimately, failure — even when the stress levels are below the material’s yield strength. This is particularly vital for components exposed to continuous operational vibrations or loads that fluctuate over time.
Key Evaluation Criteria:
- Number of load cycles before failure
- Stress-life (S-N) curves
- Damage accumulation (Miner’s rule)
- Crack propagation rate
Industries Where It’s Critical:
- Aerospace
- Automotive
- Offshore structures
- Rotating machinery
- Pipelines and pressure vessels
Why It Matters:
Fatigue failures are often sudden and occur without visible deformation. Identifying potential failure points early ensures safe operation and extends the lifecycle of equipment.
5. Buckling Analysis
Definition and Purpose:
Buckling analysis predicts the point at which a structure becomes unstable under compressive forces. When slender members (like columns, plates, or shells) are loaded beyond a critical value, they may suddenly deform laterally—a failure mode often more catastrophic than yielding.
Buckling Types:
- Elastic Buckling
- Inelastic Buckling
- Local Buckling
- Lateral-Torsional Buckling
Key Inputs:
- Geometry
- Load application points
- Boundary conditions
- Material properties
Applications:
- Tall structural columns
- Thin-walled tanks and vessels
- Base plates and stiffeners
- Frames and trusses under compression
Role of Advanced Software Tools for Industrial Structural Analysis
Structural analysis is a much more sophisticated field than spreadsheets and 2D drafting. Today’s advanced technologies combine Finite Element Analysis (FEA), 3D modeling, and multidisciplinary collaboration in engineering teams. These technologies increase accuracy, speed up project schedules, reduce design errors, and foster collaboration.
Let’s examine the practical use of a few of these tools:
- STAAD.Pro: STAAD is a popular tool for structural analysis and design. Engineers can assess a structure’s behavior under different loads and forces with the aid of Pro. Steel, concrete, timber, aluminum, and cold-formed structural analysis are all supported, and it conforms with international norms such as Eurocodes, IS, and AISC.
- Tekla Structures: Tekla allows for precise 3D representations of even the most intricate constructions and is mostly used for steel details and modeling. For steel buildings, skids, pipe racks, and modular structures that need accuracy and collaboration with fabrication teams, it is perfect.
- Navisworks & Revit: These tools are key for model coordination and clash detection. Structural engineers use them to integrate models with piping, mechanical, and electrical teams—ensuring smooth execution during construction.
- SOLIDWORKS Simulation: Integrated FEA tools for static, dynamic, thermal, and fatigue analysis allow SOLIDWORKS to expand its 3D CAD capabilities. It is especially useful for evaluating mechanical components at the part and assembly levels, allowing for iterative design modifications and verification prior to production.
- ANSYS: Exceeding linear computations, ANSYS provides FEA capabilities for comprehensive stress analysis and simulation. In load-bearing structures and important equipment supports, it aids in the analysis of fatigue, buckling, and thermal stress.
- AutoCAD Plant 3D & Civil 3D: Frequently used in tandem with structural tools, these platforms facilitate site layout, foundation interface, and piping system integration.
Rishabh Engineering’s Approach To Industrial Structural Analysis
As a multidisciplinary design engineering company, we combine deep technical expertise with leading software tools to provide end-to-end structural engineering services.
Here’s how we do it:
1. Expert Team & Proven Workflow
Our structural engineering team includes highly experienced engineers who work closely with process, piping, and electrical disciplines to deliver integrated designs. Every project follows a rigorous workflow:
- Requirement gathering
- Preliminary design and modeling
- Load definition and analysis
- Optimization and validation
- Documentation and client review
2. Software Proficiency
We use a comprehensive suite of tools including STAAD.Pro, Tekla Structures, Navisworks Manage, AutoCAD, and Revit. This allows us to model, simulate, and validate designs with confidence.
3. Scope of Services
Our structural engineering capabilities cover:
- Pipe racks and pipe bridges
- Equipment foundations and skids
- Modular platform structures
- Cold box supporting structures
- Stair towers and handrails
- Structural steel framing
- Environmental load analysis (wind, seismic, snow, transport)
We also provide foundation load tables and coordinate closely with geotechnical and civil teams.
4. Global Code Compliance
We deliver designs that comply with a wide range of international standards, including:
- American codes: AISC, ASCE, IBC, API
- Indian codes: IS 800, IS 456, IS 1893
- European codes: Eurocode 3 and 4
- Others based on project location and client requirements
Real-World Case Study
Let’s look at how Rishabh Engineering has helped clients solve complex structural challenges using advanced modeling tools.
Case Study: Cold Box Base Plate Design
Client Overview:
A global technology-driven manufacturer required structural design validation for the base plate of a cold box unit used in a cryogenic gas application. Given the critical operational environment and the need for precise load handling, they turned to Rishabh Engineering for expert analysis and base plate design support for cold box structure.
Project Objective:
To ensure the structural integrity and stability of the cold box base plate under multiple loading conditions, including:
- Equipment weight
- Wind load
- Seismic impact
- Transportation-induced stresses
Rishabh Engineering’s Scope of Work:
- 3D modeling of the base plate using Tekla
- Static structural analysis and design using STAAD.Pro Connect Edition
- Buckling and fatigue risk evaluation
- Optimization of support and anchor points
- Foundation load calculation and plate thickness validation
Analysis & Findings:
Rishabh’s structural team performed a comprehensive static and dynamic analysis of the base plate structure. Through iterative finite element simulations, they validated that the proposed design could withstand the operational and transit loads without any signs of local buckling or fatigue failure.
By examining stress concentration points and ensuring an even distribution of loads, Rishabh proposed modifications to the thickness and layout of stiffeners on the base plate. The design met both American and international structural codes, ensuring safety and compliance.
Outcome:
- Structural integrity validated under design loads
- Material savings through optimized stiffener layout
- Improved reliability during transportation and operation
- Successful compliance with client specifications and regulatory standards
Final Words
To sum up, constructing safe, effective, and durable structures for a variety of sectors requires an awareness of the several kinds of structural analysis. From simple static analysis to intricate dynamic and nonlinear assessments, every technique is essential to guarantee performance in a variety of scenarios. Companies utilize advanced technologies and engineering expertise to achieve design accuracy, reduce risks, and enhance project performance. We offer specialized structural analysis services that make use of multidisciplinary skills to guarantee complete compliance with pertinent codes. In addition to improving a structure’s strength and dependability, our method encourages cost effectiveness and functional performance in a variety of engineering applications.
Seek Help With Expert Structural Analysis For Your Next Industrial Project?
We deliver code-compliant, precision-driven designs ensuring safety, compliance, performance, and structural integrity through advanced analysis and multidisciplinary expertise.
Related Blogs
Related Blogs
Best Structural Engineering Software for Accurate Analysis
Finding tools that simplify and improve the accuracy of the…
Detailed Engineering Considerations for Project Success
Engineering projects today require meticulous planning and execution across various…