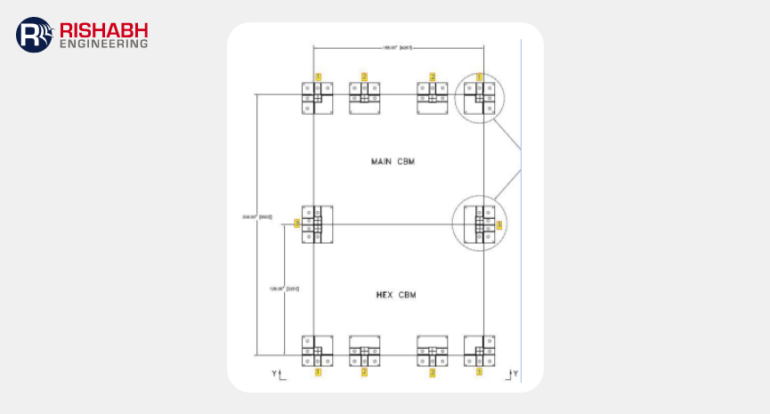
Project Information
Cold Box Base Plate Design Using FEA Method
Description
Client
A US-based manufacturer of engineered cryogenic gas processing equipment and small-scale process plants for liquefied natural gas (LNG), well services, and industrial gas industries with a significant presence in Southeast Asia.

Engineering Requirement
The client presented a meticulous engineering requirement, focusing on optimizing and analyzing various components within their project framework. Specifically, they sought a comprehensive approach to designing the Base Plate for the Cold Box Structure, a critical element that necessitates structural integrity and compliance with ASME standards.
The project’s scope was ambitious, requiring an in-depth analysis of the base plate design utilizing advanced Finite Element Analysis (FEA) methodologies. To ensure the highest quality and performance standards, the approach adopted was iterative, concentrating on Grade 52 material with a yield strength of 345 MPa. This methodical process aimed to fine-tune every design aspect to meet the project’s stringent requirements.
The deliverables outlined were extensive and precise, encompassing base plate design calculations, detailed drawings, and the crucial SE Stamping in Washington State, ensuring compliance with regulatory standards. Adherence to ASME Sec VIII, Div-2, Part 5, Edition 2021 standards was paramount throughout the project lifecycle, underscoring the commitment to excellence and safety.
In addressing this multifaceted engineering requirement, utilizing cutting-edge software tools was pivotal. STAAD.Pro facilitated robust structural analysis, while RAM Connect ensured seamless integration and optimization. Autodesk AUTOCAD provided the platform for meticulous detailing and design visualization, while NAVISWORKS enabled comprehensive project coordination and collaboration. Ansys offered advanced FEA capabilities to validate design decisions, ensuring reliability and performance. Additionally, MS Office tools streamlined documentation and communication processes, enhancing efficiency and project management. Integrating these software solutions empowered our civil & structural engineering services team to navigate complex challenges confidently, delivering innovative solutions that exceeded client expectations while adhering to the highest industry standards.
Want to know more about this project?
Our Recent Projects
Connect with us for all your engineering design needs
US Toll-Free Phone
+1-877-747-4224
India Phone
+91 8511122697
Drop Us An Email
sales@rishabheng.com
Our Offices
USA, UK & India (Head office)