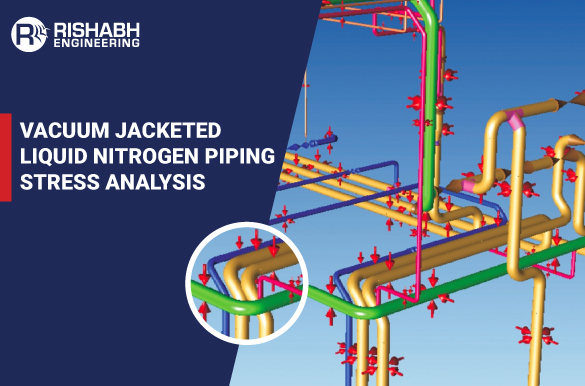
Piping Stress Analysis Of Vacuum Jacketed Liquid Nitrogen Pipes – Challenges, Benefits, Steps
|With cryogenic packages, ensuring the equipment’s structural integrity is paramount since extreme cold and high pressure converge. And one of the critical components in this domain includes vacuum-jacketed liquid nitrogen pipes. These pipes transport and maintain cryogenic liquids, such as liquid nitrogen, at ultralow temperatures and under vacuum conditions. To safeguard against catastrophic failures, pipe stress analysis emerges as a cornerstone process in their design and engineering.
In this blog post, we’ll explore the importance and intricacies of stress analysis for vacuum-jacketed liquid nitrogen pipes and the varied benefits with a real-life case study to showcase the significance of maintaining operational safety and efficiency.
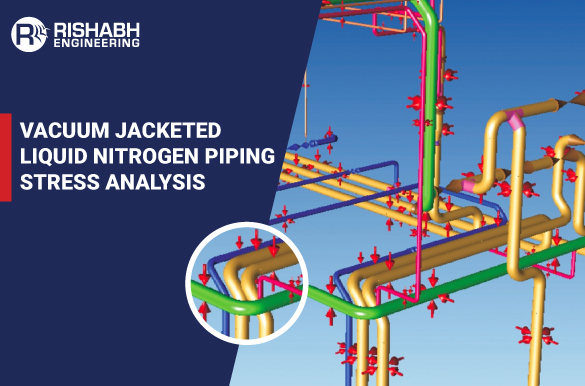
What Is Vacuum Jacketed Piping For Liquid Nitrogen Pipes?
Vacuum-jacketed liquid nitrogen pipes are constructed with an inner pipe, which carries the cryogenic fluid, surrounded by an outer jacket maintained under vacuum. This design minimizes heat transfer through conduction and convection, making them ideal for transporting and storing cryogenic liquids, which are incredibly temperature-sensitive.
Advantages of Vacuum Jacketed Pipe:
- Significant reduction in loss of liquid cryogen caused by heat leaks
- Quick return on investment in new vacuum jacketed pipe installation
- Virtually no decrease in thermal performance of vacuum jacketed pipe over ten years
- Consistent delivery of liquid nitrogen at the use points due to the reduction of vapor content
- Improved process safety due to the elimination of frosty and dripping conditions
Piping Stress Analysis for Liquid Nitrogen Pipes – Challenges Solved & Advantages
Stress analysis involves evaluating how mechanical forces, such as pressure, thermal expansion, and external loads, impact the structural integrity of materials.
Challenges Solved By Pipe Stress Analysis for Cryogenic Conditions:
With vacuum-jacketed liquid nitrogen pipes, this analysis is paramount due to the unique challenges posed by cryogenic conditions as listed below:
- Temperature Extremes: Cryogenic temperatures can cause materials to become brittle, leading to potential cracking or fracture. Stress analysis helps determine if the materials can withstand these extreme temperature fluctuations without compromising their integrity.
- Thermal Stresses: Differences in temperature between the inner and outer pipes can induce thermal stresses. Stress analysis aids in evaluating these stresses and ensures that the materials used can handle the expansion and contraction without failing.
- Vacuum Conditions: The vacuum jacket surrounding the inner pipe creates an environment of external pressure. Stress analysis accounts for this vacuum pressure and prevents the buckling or collapse of the tube under these conditions.
- Pressure Variations: Transporting cryogenic fluids involves pressure changes, which can impact the structural integrity of the pipes. Stress analysis assesses these pressure variations to ensure the pipes can withstand them without deformation or rupture.
Advantages of Comprehensive Stress Analysis with Vacuum Jacketed Liquid Nitrogen Pipes:
A thorough stress analysis of liquid nitrogen vacuum jacketed piping systems offers numerous benefits that go beyond structural integrity:
- Safety Assurance: By identifying potential failure points, stress analysis ensures the pipes can operate safely under demanding cryogenic conditions.
- Cost Efficiency: Preventing failures through stress analysis reduces the need for costly repairs or replacements, saving time and resources.
- Optimal Design: Stress analysis enables engineers to fine-tune the design, enhancing efficiency and performance while minimizing material usage.
- Regulatory Compliance: Compliance with safety regulations and standards is crucial. Stress analysis helps ensure that vacuum-jacketed liquid nitrogen pipes meet or exceed these requirements.
- Reliability: Well-analyzed pipes offer consistent performance, preventing unexpected downtimes and disruptions.
Performing Pipe Stress Analysis for Vacuum Jacketed Liquid Nitrogen Pipes:
Stress analysis of piping systems involves a series of steps to ensure that the vacuum-jacketed liquid nitrogen pipes are robust and reliable:
- Material Selection: Choosing suitable materials that can withstand extreme temperatures and pressures is crucial. Materials must also exhibit low thermal conductivity to maintain the effectiveness of the vacuum insulation.
- Finite Element Analysis (FEA): FEA is a numerical simulation method to predict how a structure will respond to various mechanical conditions. It aids in visualizing stress distribution, identifying potential weak points, and optimizing the design for maximum safety.
- Thermal Stress Assessment: Temperature differences can lead to thermal expansion or contraction, inducing stresses. Stress analysis assesses how these thermal stresses might affect the structural integrity of the pipes.
- Pressure Load Assessment: Considering the pressure variations in the pipes, stress analysis determines how the materials will respond to these changes and ensures they remain within their safe limits.
- Fatigue Analysis: Repeated pressure fluctuations and cyclic loading can lead to fatigue failure over time. Stress analysis helps predict and prevent such losses by assessing the fatigue life of the pipes.
Rishabh Engineering Pipe Stress Analysis Services Experience
We have profound experience with conducting and offering pipe stress analysis services. Our team of designers and engineers specializes in the meticulous evaluation of piping systems while ensuring their structural integrity and safety under a variety of conditions. They are skilled at utilizing advanced software like CAESAR II, AutoPIPE Ansys and more to simulate and assess stress levels within pipelines. This capability allows them to identify potential weak points, mitigate risks, and optimize designs, ultimately reducing costly operational issues and enhancing overall project efficiency. Moreover, it is our commitment to quality that extends beyond analysis, from design consultation to final implementation while ensuring that every aspect of your piping system is not just functional but also reliable in the long run.
Project Showcase: Stress Analysis of Vacuum Jacketed Liquid Nitrogen Pipes
One of our North American cryogenic gas equipment and systems manufacturers was pursuing an engineering service partner to conduct pipe stress analysis for vacuum jacketed liquid nitrogen lines for one of their existing facilities with a design temperature of -320°F and pressure of 200 PSIG.
Project Scope:
With Rishabh Engineering’s extensive experience in modeling industry gas packages, the client awarded the project to our team. Our scope for this project included the following;
- Piping Stress Analysis
- Weld strength check
- Collapse calculation
- Surge analysis
- Considering snow load
We performed weld strength checks across all welding points, having;
- Core Pipe and Jacket
- Jacket and Sleeve
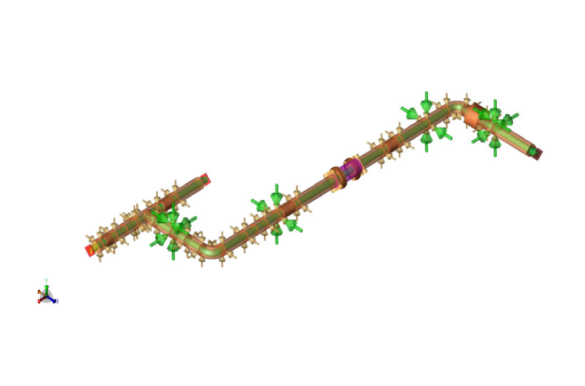
Design Parameters:
Parameters | Value |
Total Piping Systems | 25 |
Total Number of Lines | 25 |
Max. Pipe Diameter | 6″ |
Max. Temperature | -320oF |
Max. Pressure | 200 PSIG |
Software Technologies Utilized:
- Hexagon CAESAR II 2018
Final Words
In conclusion, stress analysis ensures that vacuum-jacketed liquid nitrogen pipes’ structural integrity and operational reliability are built. In the intricate imbalance between extreme cold, high pressure, and structural stability, stress analysis provides the roadmap to ensure that these critical components can withstand the harsh cryogenic environment. Through careful material selection, advanced simulation techniques, and a deep understanding of the challenges, engineers create pipelines that carry cryogenic fluids and the weight of safety, efficiency, and innovation.
Ready to Ensure Cryogenic Pipe Safety?
Our designers and engineers help conduct pipe stress analysis to safeguard your cryogenic piping systems to ensure structural integrity and operational efficiency.
Related Blogs
Related Blogs
Piping Support Design and Engineering
Pipe support design is an important component of piping engineering…
Detailed Engineering of Piping Systems
Detailed engineering involves design, detail, engineering and layout of piping…