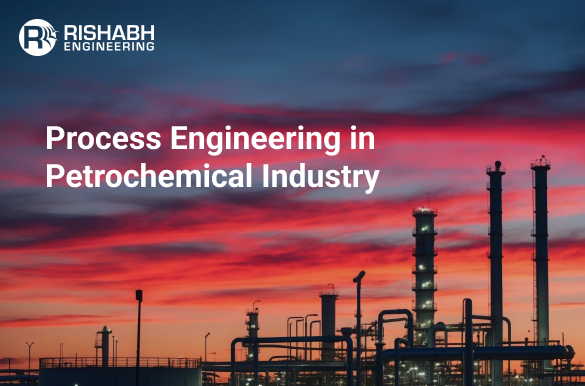
Process Engineering in Petrochemical Industry
|Engineering procedures are crucial to achieving operational excellence in the fiercely competitive and exacting petrochemical sector. Process engineering is utilized in the design and commissioning of plants to inform decisions about how to convert raw materials into useful products, maximize system throughput, and ensure safety, sustainability, and compliance with standards. The right engineering partner could mean the difference separating being successful and being unsuccessful in a situation where time is critical and margins are exceedingly tight. It is a critical competency that increases output, reduces risks, and speeds up project completion at Rishabh Engineering. Using years of experience and a tried-and-true methodology, we offer complete end-of-the-end solutions for projects in this industry of any scale.
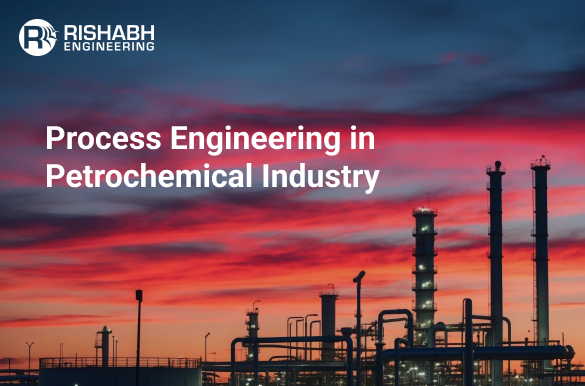
In this article, we explore the fundamental role of process engineering in petrochemical industry and how Rishabh Engineering’s process engineering discipline experience helps companies meet the ever-evolving challenges of the sector.
The Strategic Role of Process Engineering in Petrochemical Industry
The design, optimization, and control of chemical, physical, and biological processes are at the heart of this field. This would include a variety of duties necessary to meet operational goals for petrochemical complexes. Process engineers must therefore ensure that systems are safe, scalable, energy-efficient, and aligned with goals for sustainability, production, and safety.
The critical components would include:
- Reaction Engineering: This involves creating the most economical and efficient processes possible by optimizing the chemical reactions that convert raw materials into final products.
- Separation Processes: Key to separating various components and increasing product production are procedures including distillation, absorption, and extraction.
- Heat and Mass Transfer: Successful management of heat exchange and fluid dynamics ensures process stability and efficient energy use.
- Fluid Dynamics and Hydraulics: To maintain the proper flow rates, pressures, and temperatures, the system’s gas and liquid movements must be meticulously regulated.
- Equipment Sizing and Specifications: For system efficiency, it is essential to properly size and specify the appropriate equipment, such as compressors, heat exchangers, and reactors.
- Sustainability and Energy Integration: Petrochemical plants need intelligent energy management systems that maximize resource use, lower emissions, and enhance environmental sustainability.
Process engineering must provide a system that is safe, economical, scalable, environmentally friendly, and able to satisfy production goals. Process engineers must decide on system layout, material handling, energy consumption, and automation while strictly adhering to regulatory standards, whether they are revamping an old plant (brownfield) or beginning from scratch with a new facility (greenfield). Explore how Rishabh Engineering helps companies with process engineering to conceptualize, design, and optimize operations.
Key Challenges in the Petrochemical Sector
The projects in this industry face a range of challenges, many of which are unique to the sector:
- Tight Regulatory Compliance: Emissions, safety, and waste disposal standards are increasingly strict and subject to frequent revisions. The complex compliance environment requires engineers to be vigilant in both design and operation to avoid costly fines and shutdowns.
- Complex Chemistry and Catalysis: Petrochemical plants often deal with sophisticated feedstocks, catalysts, and reactions that require intricate modeling to ensure optimal performance. Even slight deviations from the ideal process conditions can result in reduced yields and increased costs.
- Capital and Operational Expenditure Pressure: Petrochemical companies are under constant pressure to increase output while reducing capital expenditure (CapEx) and operating costs (OpEx). This demand for higher performance with fewer resources makes process engineering even more crucial.
- Digital Integration: With the rise of digital technologies, petrochemical engineers now must incorporate real-time process data, digital twins, and predictive maintenance strategies to optimize performance and minimize downtime.
- Global Collaboration: Large petrochemical projects often span multiple geographies, time zones, and cultures, which complicate coordination and delivery. Effective project management and communication between global teams are critical for success.
At Rishabh Engineering, they are seen as roadblocks but as opportunities to provide value through targeted solutions. By leveraging its vast expertise and advanced tools, Rishabh delivers optimized systems that meet both technical and financial requirements.
How Rishabh Engineering Adds Value at Every Stage Of Petrochemical Process Engineering?
Our team offers a wide range of services across varied disciplines tailored specifically to meet the demands of the petrochemical industry. The company combines technical expertise and software capability, thus ensuring the delivery of reliable, efficient, and cost-effective solutions. Here’s a breakdown of how Rishabh Engineering supports clients throughout every stage of projects.
1. Front-End Engineering Design (FEED):
The foundation for any project’s successful completion is laid during the FEED phase. To reduce the possibility of scope revisions and maintain budgetary stability, we concentrate on developing a clear and accurate design during this phase. Here’s how our staff at Rishabh Engineering makes sure everything runs smoothly and effectively:
- Process Flow Diagrams (PFDs): Our engineers produce neatly structured process flow diagrams (PFDs) that show the complete procedure and make sure all the parts work together properly. This step considers energy, material flow, and safety, all of which are critical to the overall functioning of the system.
- Piping & Instrumentation Diagrams (P&IDs): P&IDs, or pipe and instrumentation diagrams, are comprehensive diagrams that aid in defining the configuration of instrumentation and piping systems and promote effective multidisciplinary communication.
- Mass and Energy Balances: By calculating the material and energy flows, one can make sure that all inputs and outputs are taken into consideration, which aids in performance and energy usage prediction.
- Preliminary Equipment Sizing: We help clients determine the optimal size and specifications for equipment, including reactors, compressors, and separators, ensuring scalability and efficiency.
- Technology Assessment and Selection: Our engineers conduct thorough assessments to identify the most suitable technologies, based on the project’s unique needs and challenges.
By addressing key design considerations early in the project lifecycle, Rishabh Engineering ensures that clients have a solid foundation to build upon, minimizing risk and improving budget accuracy.
2. Detailed Engineering
After the FEED phase, during the detailed engineering phase precise calculations and specifications are vital. Rishabh Engineering provides:
- Heat and Material Balances (HMBs): By adjusting energy consumption and material flow, these computations ensure that resources are used effectively, and waste is kept to a minimum.
- Utility Consumption Reports: We can optimize energy and water use and create a more environmentally friendly organization by precisely monitoring utility needs.
- Line Sizing and Pressure Drop Calculations: Maintaining efficiency and dependability requires carefully planning piping systems to guarantee smooth flow and low-pressure loss.
- Design of Relief Valve and Flare Systems: To manage crises in a safe and efficient manner, our skilled staff concentrate on creating safety systems, such as flare systems and pressure relief valves.
- Control Philosophy and Logic Development: We create dependable and transparent control plans that guarantee operations remain within safe and ideal bounds even in the face of shifting circumstances.
Rishabh Engineering offers focused detailed engineering services that align with industry code & standards thus ensuring that that the project meet operational and regulatory requirements while optimizing costs and performance for the client.
3. Simulation and Modeling
Simulation tools are essential for improving plant performance, and process optimization is a continuous process. At Rishabh Engineering, we employ cutting-edge process modeling technologies to promote advancements in several crucial areas:
- Identification and Elimination of Bottlenecks: To improve overall throughput and operational efficiency, we focus on identifying bottlenecks in the system and taking appropriate corrective actions.
- Energy Optimization and Pinch Analysis: By recovering waste heat and improving thermal performance, our team helps clients optimize energy efficiency and minimize costs and environmental effects.
- Debottlenecking and System Revamping: To assist plants in boosting capacity and enhancing performance without requiring a total redesign, our skilled engineers conduct in-depth analyses to identify opportunities for system upgrades.
- Dynamic Simulation for Process Control: Our team helps clients better understand system behavior, optimize operations, and enhance process control by simulating dynamic process circumstances.
Plant operators may make well-informed, data-driven decisions thanks to this sophisticated simulation and modeling technique, which enhances performance and lowers risk. Our technical team makes sure that all design elements interact seamlessly, preventing conflicts and minimizing rework, by utilizing industry-leading software platforms.
4. HAZOP and Risk Analysis
In the petrochemical sector, safety is of utmost importance. At Rishabh Engineering, we concentrate on anticipating and mitigating such hazards before they become issues. To do this, we employ several crucial safety procedures:
- Hazard and Operability Studies (HAZOP): By using a systematic method, we may reduce risks from the outset by identifying possible hazards and operational difficulties early in the design phase.
- Failure Mode and Effects Analysis (FMEA): This technique allows us to forecast potential points of failure in systems or equipment. This allows us to make design changes that increase overall safety by reducing the possibility of these failures.
- Design of Safety Instrumented Systems (SIS): We assist clients in adhering to industry safety regulations by designing safety systems that guard against catastrophic failures.
- Analysis of the Layer of Protection (LOPA): By identifying layers of protection against dangers, this strategy makes sure that a plant can function safely in a variety of situations.
By identifying risks early in the project lifecycle, Rishabh Engineering helps clients avoid costly shutdowns, improve safety margins, and ensure compliance with OSHA, EPA, and other safety regulations.
5. Revamp and Retrofit Projects
Brownfield projects require specialized expertise in revamping existing facilities. Rishabh Engineering team excels at retrofitting and upgrading legacy systems by:
- Reverse Engineering Legacy Systems: For older plants, we apply a reverse engineering approach to understand existing systems and identify areas for improvement.
- Feasibility Studies for Capacity Upgrades: Without requiring a complete plant layout, our team assesses the possibility of upgrading current units to meet new production targets.
- Modular Integration: We guarantee a seamless integration of new units into an existing system without interfering with factory operations.
By executing revamp projects with minimal downtime, Rishabh Engineering extends the life of existing assets, helping clients maximize the return on investment.
6. Global Delivery Model
Rishabh Engineering’s global delivery model includes teams located in India, providing clients with significant cost efficiencies and access to world-class engineering talent. With experience working across time zones and diverse geographies, we offer:
- Scalable Teams: Our team enables you to meet the specific scope of each project, whether it’s a small upgrade or a large-scale greenfield project.
- Time Zone-Aligned Execution: By aligning our work schedule, our team ensures accurate progress on projects.
- Cost Efficiency: Offshore execution helps clients achieve high-quality results at a competitive price point.
Final Thoughts
A reliable partner for petrochemical process design, Rishabh Engineering provides creative, all-inclusive, and expandable solutions that propel project success. The operations of this industry are non-negotiable, demanding performance and accuracy. Specialized process engineering services are therefore required to ensure efficiency, scalability, and safety. Whether you’re beginning from scratch, retrofitting an existing facility, or integrating state-of-the-art digital technology, Rishabh Engineering’s knowledge, tools, and flexible execution style guarantee that your projects are finished safely, precisely, and within your allocated budget. Businesses who collaborate with our team usually get a competitive advantage in an industry where operational efficiency and regulatory compliance are essential, allowing them to thrive in an increasingly complex global economy.
Partner With Experts In Process Engineering
Our team helps optimize your petrochemical projects with precision & efficiency.
Related Blogs
Related Blogs
Process Modeling & Simulation Using AspenTech Software in Multidisciplinary Engineering
For the ever-evolving world of industrial processes and engineering, the…
Navigating the World of Process Engineering with Rishabh Engineering
Process engineering can be considered the foundation for modern manufacturing,…