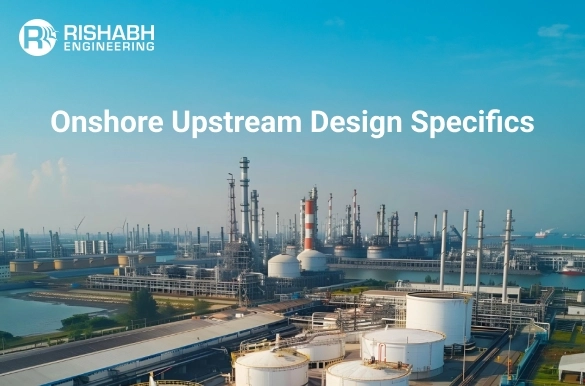
Onshore Upstream Facility Design Essentials
|Exploration and production efforts are still being driven by the expanding demand for gas and oil onshore and offshore worldwide. Onshore upstream design is essential for the extraction of hydrocarbons from land-based reservoirs. It guarantees the process’s efficiency, safety, and environmental responsibility. The planning of surface infrastructure and safety systems, wells, and the smooth integration of several technical systems are all included in this field of engineering.
This article will go over the different aspects of onshore upstream facility design, its components, key considerations, along with potential challenges and best practices.
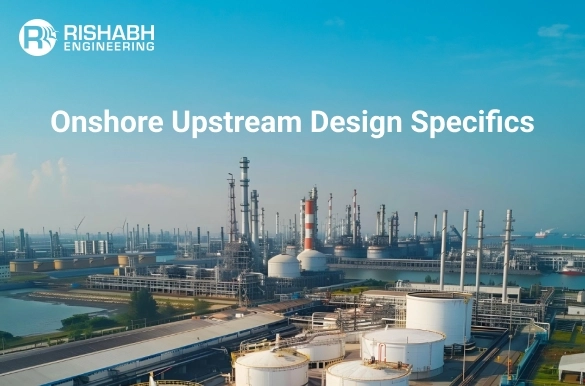
What is Onshore Upstream Facility Design?
Building all the infrastructure required to extract gas and oil from the earth on land is known as onshore upstream facility design. To help get the resources out, process them, and get them to their destination, systems must be planned, engineered, and constructed. Onshore setups must cope with issues such land conditions, roads, local legislation, and the potential impact of the construction on neighboring people, in contrast to offshore facilities that are constructed in the water. Further, to keep expenses down and minimize environmental damage, the primary goal is to ensure that oil and gas are handled safely and effectively.
Components of Onshore Upstream Facilities
This type of facility consists of multiple interdependent components that work together to enable efficient oil and gas production.
Key components include:
- Wellheads & Gathering Systems: This is the first place where hydrocarbons leave the reservoir. They consist of control systems, flowlines, and valves.
- Separation Units: The production stream is separated into water, gas, and oil for subsequent processing using separators.
- Processing Units: To condition the raw production stream, facilities like heater treaters, gas treatment plants, and oil dehydration units are crucial.
- Storage Tanks: Prior to being transported, water and crude oil are momentarily kept in above-ground tanks.
- Pipeline Infrastructure: Products are transported to processing plants or export destinations via internal and external pipelines.
- Utility Systems: These comprise instrumentation, communication systems, chemical injection, water treatment, and electricity generating.
- Flare and Vent Systems: Made to discharge or burn extra gases in a regulated manner during startup, shutdown, or emergency scenarios.
- Control Rooms & Safety Systems: Centralized locations where automated safety shutdowns can be started and operations are tracked.
- Infrastructure Support: Roads, fences, lighting, drainage, and accommodations where needed are all examples of infrastructure support.
Onshore Upstream Facility Design Considerations
For such a facility, you need to consider varied technical, environmental, and operational factors to ensure optimal performance.
Key considerations include:
- Knowing the Reservoir: The type of equipment and materials required to build the reservoir depend on the underground pressure, temperature, and type of gas or oil.
- Planning for Production: Engineers can determine the size of storage tanks, separators, and pipelines by projecting the amount of oil or gas that will flow out.
- Room to Grow: Depending on how output changes over time, facilities are typically constructed to be easily extended or shrunk.
- Environmental Compliance: Models must adhere to local and international environmental standards related to emissions, water usage, and waste management.
- Energy Efficiency: Minimizing energy use while maximizing recovery improves operational economics and reduces carbon footprint.
- Local Terrain and Accessibility: Site layout must consider land gradients, flood zones, seismic activity, and logistics for transportation.
- Corrosion and Material Degradation: Selection of materials that resist corrosive substances (like H₂S or CO₂) is vital for safety and longevity.
- Automation and Digital Integration: Facilities should include smart instrumentation and control systems for real-time monitoring and performance optimization.
- Health and Safety Standards: It must incorporate fire and gas detection, emergency shutdown systems, and personnel safety features.
Challenges in Upstream Facility Design
This type of facility poses several challenges that engineers, and project teams must navigate:
- Remote and Harsh Environments: Many oil and gas fields are in difficult-to-access areas with limited infrastructure and extreme weather.
- Regulatory Hurdles: Navigating complex environmental and land-use regulations can delay project timelines or increase costs.
- Material Selection Under Harsh Conditions: Facilities must handle high pressures, temperatures, and corrosive agents, requiring advanced materials.
- Uncertain Reservoir Performance: Actual reservoir behavior may differ from forecasts, affecting facility sizing and production planning.
- Operational Safety Risks: Poorly designed systems can lead to blowouts, leaks, fires, and other hazardous incidents.
- Supply Chain Limitations: Delays in equipment procurement or logistics challenges in remote locations can disrupt project schedules.
- Integration Across Disciplines: Coordination among civil, mechanical, electrical, and instrumentation teams is essential but often complex.
- Cost Control: Balancing capital expenditure with operational reliability and efficiency remains a key financial challenge.
How Rishabh Engineering Team Helps with Onshore Upstream Facility Design?
The design and construction of onshore upstream infrastructure is supported by Rishabh Engineering’s practical, value-driven approach and extensive multidisciplinary knowledge. The team guarantees technically sound, safe, compliant, and economical optimization at every phase thanks to their solid track record in oil and gas engineering services.
Here’s how Rishabh Engineering adds value across various phases:
Multidisciplinary Engineering Support:
Rishabh’s team comprises experienced professionals from multiple disciplines — including process, mechanical, piping, civil & structural, electrical, and instrumentation. The multidisciplinary engineering services team approach ensures that all systems work seamlessly together, avoiding delays and rework during execution.
Front-End Engineering and Design (FEED):
The team specializes in detailed FEED studies that help operators make informed investment decisions. Through accurate planning, layout optimization, and cost estimation, Rishabh Engineering supports project owners in reducing uncertainties and planning for scalable facility development.
Well Pad & Flowline Design:
Our team supports with well pad layout planning, flowline routing, tie-in point identification, and infrastructure connectivity. The focus is on minimizing environmental disruption while ensuring efficient flow of hydrocarbons to the central processing facilities.
Surface Facility Engineering:
The team models all major surface facilities, including:
- Oil and gas separation units
- Dehydration and sweetening systems
- Compressors and pumps
- Heater treaters and storage tanks
- Flare and vent systems
They are developed using advanced tools like AutoCAD Plant 3D, CADWorx, and Navisworks for accurate layout and clash detection.
Piping & Pipeline Engineering:
Our team conducts piping stress analysis (using CAESAR II), material selection, and routing analysis to ensure safe and efficient hydrocarbon transport. This includes design for internal process piping as well as external pipeline networks connecting to storage or transport hubs.
Structural & Foundation Design:
The team delivers civil and structural design for pipe racks, equipment foundations, shelters, and buildings. They are developed using STAAD.Pro and TEKLA to meet seismic, wind, and soil conditions while complying with international building codes.
Instrumentation & Electrical Design:
The instrumentation engineering services team executes the complete modeling and specification of control systems, field instrumentation, and electrical systems including power distribution, lighting, earthing, and emergency systems. While the electrical engineering services team works on integrating the remote monitoring systems.
HSE and Compliance Integration:
Health, safety, and environmental (HSE) design is embedded into every stage of the facility’s plan. Rishabh’s team ensures that all layouts adhere to local and international codes such as API, ASME, OSHA, and environmental emission standards. Risk assessments and hazard mitigation strategies are also included in the package.
3D Modeling and Design Reviews:
To enhance accuracy and client collaboration, the team offers full 3D plant modeling and walk-throughs, which help stakeholders visualize layouts, identify potential issues early, and finalize plans efficiently.
Project Management and Documentation:
Our team promptly creates comprehensive documentation, including:
- Design calculation sheets
- Bill of materials (BOM)
- Equipment and material specifications
- As-built drawings and layout plans
- Schedules and progress reports
This ensures transparency and traceability across the project lifecycle.
International Experience with Regional Adaptability:
With a global client base, Rishabh Engineering has experience working on diverse geological terrains and regulatory environments — from North America and the Middle East to Southeast Asia and Africa. The team adapts to suit specific regional constraints and client expectations.
Value Engineering and Cost Optimization:
Rishabh Engineering team proactively identifies opportunities to reduce capital and operational expenditure through:
- Optimal layout planning
- Efficient material use
- Modular design strategies
- Standardization of components
This ensures long-term ROI while maintaining operational safety and performance.
Best Practices for Onshore Upstream Facility Design
To overcome challenges and deliver high-performance facility, industry leaders follow several best practices:
- FEED: Putting time and money into thorough front-end preparation increases the precision of technical, scheduling, and budgetary decisions.
- Modular Design Approach: Prefabricated and modularized solutions improve quality control while cutting costs and time associated with field building.
- Multidisciplinary Coordination: Comprehensive and cohesive models are ensured by integrated teams comprising process, mechanical, electrical, and structural disciplines.
- Digital Tools & Simulation: Improved visualization, clash detection, and predictive maintenance planning are made possible by the use of digital twins, 3D modeling, and process simulation.
- Robust HSE Framework: Incorporate layers of protection, fire and gas systems, and emergency response plans from the start.
- Sustainable Design Elements: Incorporate renewable energy integration, flare gas recovery systems, and water recycling technologies.
- Maintain the design’s adaptability: As manufacturing increases, technology advances, or market demands shift, be prepared to modify the design.
- Vendor & Stakeholder Collaboration: Early involvement of important partners To prevent delays and ensure that everyone is on the same page, work closely with suppliers, local authorities, and other important actors from the beginning.
- Standardization Where Possible: When feasible, use shared parts: Using common tools and materials speeds up the design process and facilitates quicker acquisition.
Final Words
Multidiscipline design engineering is essential to close the gap between upstream production and downstream utilization in this dynamic environment. Safe, effective, and economical transportation of hydrocarbons is ensured by engineering teams into the early stages of onshore projects. This connection promotes long-term sustainability in achieving objectives to improve project performance. And, by employing the services of a specialist engineering services provider, one can be rest assured to implement robust & future-ready onshore upstream solutions since the demand for cleaner energy and smarter infrastructure increases.
Seek Help With Onshore Upstream Design?
Partner with our team to streamline your onshore oil & gas infrastructure for reliable and future-ready upstream facility designs.
Related Blogs
Related Blogs
Best Structural Engineering Software for Accurate Analysis
Finding tools that simplify and improve the accuracy of the…
Detailed Engineering Considerations for Project Success
Engineering projects today require meticulous planning and execution across various…