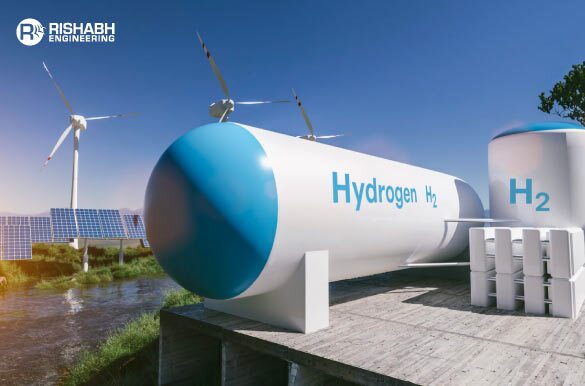
Green Hydrogen Production & Future of Sustainable Energy
|As the world accelerates toward net-zero emissions, green hydrogen is taking center stage as a clean, flexible, and scalable energy carrier. Once considered niche, it has now become a core part of global decarbonization strategies across sectors and geographies.
This blog will explore the current state of green hydrogen production, its benefits, process, key advancements, and Rishabh Engineering’s strides to harness its potential to revolutionize the energy landscape and address climate change challenges.
What is Green Hydrogen?
Green Hydrogen, often called renewable Hydrogen, is produced through water electrolysis using renewable electricity, such as solar or wind power. Unlike conventional hydrogen production methods, which rely on fossil fuels, green hydrogen offers a carbon-neutral alternative with zero greenhouse gas emissions. The global push for decarbonization, coupled with advancements in renewable energy technologies, has propelled the rapid growth of green hydrogen production in recent years.
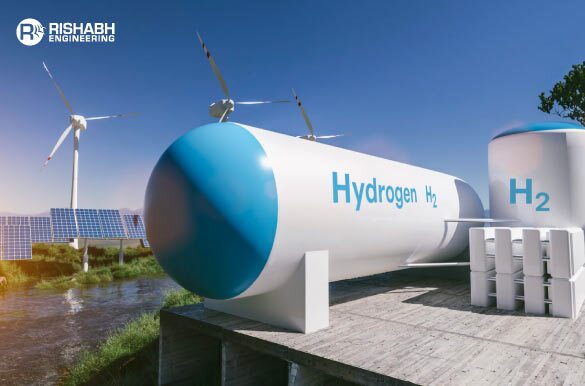
Why Production of Green Hydrogen Is Gaining Global Momentum?
It is produced using renewable electricity via electrolysis and is now seen as the missing link for decarbonizing hard-to-abate sectors—like steel, cement, shipping, and aviation—where electrification alone isn’t viable. In 2025, it is also being embraced as a strategic energy commodity that could reshape global energy trade.
Listed below are key benefits of Green Hydrogen;
- Reduced Carbon Emissions: Unlike fossil fuels, green hydrogen production is carbon-free, contributing to a significant reduction in greenhouse gas emissions during both production and use.
- Renewable Energy Integration: Green hydrogen production is closely linked with renewable sources, helping to balance supply and demand while maximizing the use of clean energy.
- Energy Storage: Green hydrogen can be stored and transported, providing a reliable energy source during periods when renewable energy generation is low, thereby enhancing grid stability.
- Decarbonization of Hard-to-Electrify Sectors: Green hydrogen plays a key role in decarbonizing industries like steel, cement, and long-haul transportation, where direct electrification is difficult.
- Energy Security: By reducing reliance on fossil fuels, green hydrogen strengthens energy security and mitigates risks tied to fluctuating fossil fuel markets.
- Versatility: It can be used in various sectors such as transportation, industry, and power generation, making it a highly flexible energy source.
- Geopolitical Stability: Reducing dependence on fossil fuel imports enhances geopolitical stability, lowering vulnerability to global supply chain disruptions.
Green Hydrogen Production Process & Key Components
A green H2 production plant is built around several critical components, each of which plays a pivotal role in ensuring the plant’s efficiency, safety, and reliability. Here’s a closer look at the essential elements that come together:
1. Production:
The electrolyzer, a device at the core of a green hydrogen plant, uses energy produced from renewable sources like solar or wind to split water (H2O) into hydrogen (H2) and oxygen (O2). Green hydrogen gets its name from this electrolysis technique, which creates hydrogen using clean, green energy without releasing carbon dioxide or other pollutants. And, at present there are varied advancements in electrolysis technology. Green hydrogen electrolysis approaches incorporate advanced materials, such as solid oxide electrolyzers and proton exchange membrane electrolyzers. It thus increases the efficiency of hydrogen production while reducing energy consumption. And, while technological advancements are continuously evolving & breakthroughs may have occurred, it is important that you make a note of the most significant ones listed below;
- High-temperature electrolysis: As the name suggests operates at elevated temperatures, typically above 500°C (932°F). Since higher temperatures facilitate faster reactions and lower the electrical input required, this approach helps improve efficiency and reduce energy consumption.
- Solid oxide electrolysis cells (SOEC): Refers to using solid oxide ceramic materials as the electrolyte. It enables better efficiency and lower energy costs even while operating at higher temperatures, up to 800°C to 1000°C (1472°F to 1832°F).
- Proton exchange membrane electrolysis (PEM): This method has gained significant interest because of its higher efficiency and faster response times. It allows only protons to pass through by utilizing a solid polymer electrolyte membrane that reduces gas crossover.
Separation & Filtration:
It is crucial to separate hydrogen from any remaining gases or contaminants after it has been created. Here’s when filtration and separation are useful. This hydrogen output is purified and now free of oxygen or other gases that may have mingled during the electrolysis process thanks to specialized equipment. From energy storage to industrial processes, this phase guarantees that hydrogen is prepared for use in a variety of applications.
Purification:
Even though filtration gets rid of most impurities, more purification is frequently needed to get the right amount of hydrogen purity. This is accomplished by refining hydrogen and eliminating minute amounts of contaminants through chemical procedures and sophisticated membrane technologies. For businesses like fuel cells and semiconductor manufacturing that depend on hydrogen for delicate processes, high-purity hydrogen is crucial.
Compression:
Hydrogen is a low-density gas, making it difficult to store and transport without first compressing it. In this stage, the hydrogen is pressurized using compressors, which condense the gas into a manageable form for storage and distribution. The compression process is vital for ensuring that hydrogen can be stored in smaller volumes, maximizing efficiency during transportation and reducing storage costs.
Storage & Transportation:
After being created, refined, and compressed, hydrogen must be safely kept until it is needed. Hydrogen may be safely contained under high pressure thanks to specialized storage tanks or containers. In order to deliver hydrogen to end customers or integrate it with energy grids, pipeline infrastructure might also be required for large-scale projects. Because hydrogen is extremely combustible, the transportation system needs to be dependable and leak-proof to guarantee that the gas stays intact while lowering the dangers.
Each of these components as part of the process of green hydrogen production must be carefully designed and integrated, requiring expertise in mechanical, electrical, and chemical engineering, making the role of a multidisciplinary design engineering company crucial in the successful implementation of green hydrogen projects. Explore this blog if you wish to learn about green hydrogen value chain and key steps involved.
How Rishabh Engineering Supports the Green Hydrogen Generation Economy?
Through our support for businesses looking to enter the hydrogen market, we are contributing to the development of clean energy’s future. This is how we change things:
- End-to-end engineering support: From FEED (Front-End Engineering Design) to detailed design, we cover all aspects—mechanical, piping, civil & structural, electrical, and instrumentation.
- Smarter plant layouts: We assist customers in creating hydrogen facilities that are more effective by maximizing available space, cutting down on material waste, and enhancing operational flow.
- Hydrogen BoP system design: We make sure that the Balance of Plant (BoP) systems are developed with the right considerations & tools that offer performance, dependability, and smooth interaction with essential technologies such as electrolyzers.
- Code and safety compliance made simple: We make it easier to navigate industry laws, safety standards, and regulations, keeping your project safe and compliant.
Real Life Case Study
We at Rishabh Engineering are instrumental in helping one such customer engaged in the production of hydrogen & ammonia by utilizing renewable energy.
Listed below are a few highlights from the green hydrogen production project;
Overview:
Engaged by one of India’s largest solar energy farm owners & operators, we are involved as green hydrogen consultants to develop their first ever “Green Hydrogen” Plant in India with a 200 NM3/hr capacity.
Project Scope:
Our scope involves detailed engineering of the BoP & technology integration supplied by the Electrolyser OEM and various packages offered by the OEM, including process compressed air packages, fire fighting systems, and more. Further, it requires everything from strategy to detailed engineering (including mechanical, piping, civil & structural, electrical, and instrumentation).
1. Layout Development
- Hazardous Area Classification
- Utility Consumption Summary and UID
2. Extended basic & detailed engineering
- Mechanical:
– Preparation of Mechanical Datasheet and RFQ for;
1) Buffer tanks
2) Various Packages such As Cooling tower, D.M., Compressor etc. - Piping:
– Developing 3D Model
– Preparation of Plot plant considering various statutory requirements and various engineering norms and standard
– Design of Fire Fighting Package for the entire facility - Civil and Structural:
– Finalize Civil design Philosophy based on Soil testing report and Site Contour survey data
– Complete Civil design for the entire Greenfield Site
– Preparation of Civil BOQ and Civil Tender. - Electrical:
– Preparation of Electrical Load list
– Complete electrical design for the entire Greenfield Site
– Preparation of electrical BOQ and electrical tender - Instrumentation:
– Preparation of Instrumentation Index and I-O List
– Control Philosophy with Integration with technology package
– Preparation of electrical BOQ and electrical Tender
3. Integrating technology package
- Review of the Technology Package (Electrolyzer unit) received from the Technology supplier
- Operating & Control Philosophy Preparation and its Integration with Technology Package
4. Technology software & professional support for BOP
5. Usage of renewable hybrid power ( Solar + Wind)
6. Hydrogen storage & filling
7. Statutory Compliance & offline support
Challenges Addressed:
- A Greenfield project with no existing facility available except solar power
- Managing safety requirements during the generation, handling & transportation of Hydrogen & Oxygen at high pressure
- Operating & Control philosophy for BOP & its Integration with the Technology package
Software Technologies Utilized:
- AutoCAD Plant 3D /Cad works: 3D Model Preparation
- Navisworks/Autodesk 2020: 3D Model Review
- AutoCAD, Acrobat Reader: Drafting and Review
- MS Excel: Line list, PMS, MTO
- STAAD.PRO: Structural Analysis
2025: Where Are We Now in the Green Hydrogen Production Phase?
Electrolyzer Innovation & Scale
- Commercial-scale projects use advanced PEM and Alkaline electrolyzers, while Solid Oxide and AEM are entering niche high-efficiency applications.
- Several giga factories are operational globally, bringing down costs and ensuring availability.
Integration with Renewables
- New facilities are co-located with wind and solar farms to ensure real-time, low-cost green power for electrolysis.
- Hybrid renewable grids with storage are enhancing hydrogen plants in the uptime.
Cost Curve Is Coming Down
- As of 2025, green hydrogen production costs are moving closer to the $1.5–2.0/kg range in high-resource areas, making it competitive with grey and blue hydrogen in some markets.
Challenges in Producing Green Hydrogen
- Water scarcity: Pushing the need for innovations in seawater electrolysis.
- Lack of transport infrastructure: Pipeline, shipping, and refueling networks are still under development.
- Skills & supply chain gaps: A global workforce and local sourcing strategy will be needed to scale responsibly.
Looking to 2030: Hydrogen's Expanding Role
In the coming years, green hydrogen is expected to:
- Support seasonal storage for renewables in power grids
- Be central to e-fuels (ammonia, methanol, synthetic kerosene)
- Integrate with carbon capture to produce ultra-clean fuels
- Enable circular economies through waste-to-hydrogen and biogenic sources
It is also anticipated to account for 12–15% of global final energy demand by 2050, making today’s investments and engineering decisions critical.
Final Words
Green hydrogen has enormous potential as an essential component of a sustainable future because of its capacity to lower carbon emissions, facilitate the integration of renewable energy, and decarbonize industries that are difficult to electrify. Rishabh engineering assists businesses with the design, optimization, and deployment of effective hydrogen systems with an emphasis on performance, safety, and compliance. Explore how we can help you on your path to a cleaner, more resilient energy future.
Seek Help with Catalyzing Green Hydrogen Production?
We can help you embrace the future of clean energy with green Hydrogen while contributing to a sustainable world.