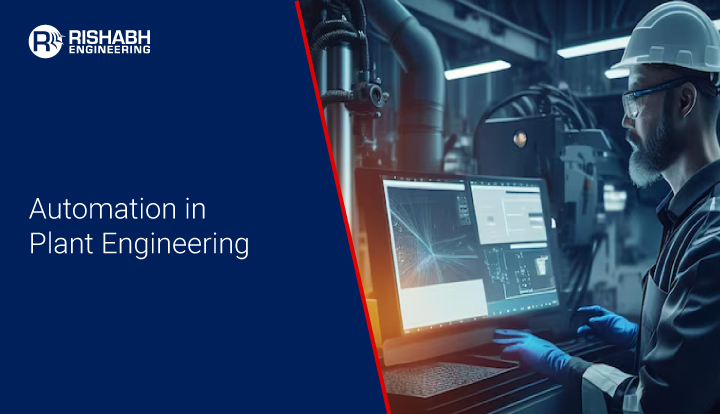
Automation in Plant Engineering: Benefits and Steps
|Plant engineering emerges as a vanguard of innovation in the dynamic realm of industrial processes. Automation is now indispensable for enhancing efficiency, safety, and sustainability. This shift isn’t just a trend but a vital necessity, safeguarding industries’ competitiveness and resilience amid intricate challenges.
Join us in this blog as we delve into the pivotal role of automation in plant engineering, spotlighting how Rishabh Engineering, with its expertise, leads the way in this transformative expedition.
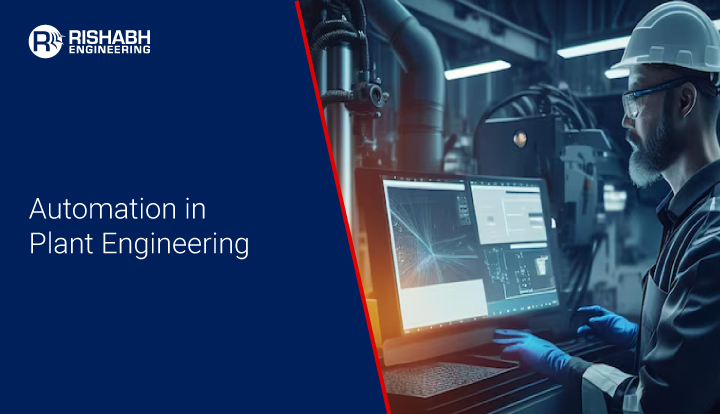
The Evolution of Automation in Plant Engineering
From manual labor to sophisticated automation, plant engineering has evolved. Incorporating sensors, actuators, control systems, and artificial intelligence optimizes operations.
- Process Optimization: Rishabh Engineering’s commitment to automation is evident in its approach to process optimization. By incorporating advanced control systems, machine learning algorithms, and real-time monitoring, the company has efficiently optimized industrial processes, improving operational efficiency, reducing waste, and mitigating the environmental impact of industrial activities.
- Digital Twin Technology: The concept of a digital twin, a virtual representation of a physical system or process, is a critical component of Rishabh Engineering’s automation strategy. By creating digital replicas of plant components and systems, engineers can simulate and analyze performance in real time, allowing for predictive maintenance and troubleshooting. This proactive approach significantly reduces downtime and maintenance costs.
- SCADA Systems Implementation: Supervisory Control and Data Acquisition (SCADA) systems are pivotal in the automation journey. Rishabh Engineering excels in implementing SCADA systems, providing industries with a centralized platform for monitoring, controlling, and optimizing various processes. This real-time visibility ensures quick decision-making and precise control over plant operations.
Key Benefits of Automation in Plant Engineering
- Increased Efficiency: Automation enhances operational efficiency by minimizing downtime, optimizing production processes, and reducing the time required for various tasks. Automated systems can operate 24/7, ensuring continuous production without regular breaks.
- Precision and Accuracy: Automation eliminates the margin of error associated with manual operations. Computerized systems can execute tasks with unparalleled precision, resulting in higher-quality outputs and reduced waste.
- Improved Safety: Automated systems handle hazardous tasks and mitigate risks associated with dangerous environments. Human operators can be spared from exposure to potentially harmful conditions, leading to a safer working environment.
- Cost Savings: While the initial investment in automation technology may be substantial, the long-term benefits include significant cost savings. Automated systems reduce labor costs, minimize errors, and optimize resource utilization, ultimately contributing to a more cost-effective operation.
How to Automate Plant Engineering?
Automating plant engineering involves implementing technologies and processes to streamline operations, improve efficiency, and reduce manual interventions. Here are steps and considerations for automating plant engineering:
- Step 1 – Assessment of Current Processes: It helps identify areas that can benefit from automation. It would include analysis of workflow bottlenecks and tracking repetitive tasks along with manual processes that can be optimized through automation.
- Step 2 – Define Automation Objectives: It would enable defining the scope for the initiative, including improving efficiency, reducing errors, enhancing safety, or increasing production capacity.
- Step 3 – Integration of Control Systems: You would agree that seamless integration between different control systems enables the creation of a unified and interoperable automation environment. This would support managing and regulating industrial processes after implementing programmable logic controllers (PLCs), distributed control systems (DCS), and other automation controllers to manage and regulate industrial processes.
- Step 4 – Sensor Integration for Data Collection: As the next step to collect real-time data, it is essential to install sensors and instruments on various aspects of plant operations, such as temperature, pressure, flow rates, and quality parameters. Further, connecting these sensors to a centralized system offers continuous monitoring and analysis.
- Step 5 – IoT and Connectivity: The Internet of Things (IoT) application to connect devices and equipment would allow remote monitoring and control. Further, it would help to safeguard sensitive plant data and prevent unauthorized access while implementing robust cybersecurity measures.
- Step 6 – Data Analytics and Machine Learning: You can derive insights from the collected data using data analytics and machine learning algorithms. Further, predictive maintenance models can be employed to anticipate equipment failures to minimize downtime and extend the machinery’s lifespan.
- Step 7 – Robotics and Autonomous Systems: Integrating robotic systems helps automate repetitive, dangerous tasks that require precision. Further, the application of autonomous vehicles or drones supports inspections and surveillance in large plant environment setups.
- Step 8 – Workflow Automation: Integrating workflow automation helps implement software solutions while enabling the seamless coordination of tasks and processes. It would include automating routine administrative tasks, document management, and reporting processes.
- Step 9 – Human-Machine Interface (HMI): Developing an intuitive and user-friendly HMI is viable to facilitate interaction between operators and automated systems. It helps to effectively use and monitor the automated systems and provide training to operators.
- Step 10 – Energy Management Systems: Integrating energy management systems helps optimize energy consumption and reduce energy costs. This is while implementing energy-efficient technologies and monitoring energy usage patterns for further improvements.
- Step 11 – Compliance and Regulatory Considerations: It is vital to keep in check with industry regulations and safety standards to ensure that the automation processes comply with local and global norms. Further, regular updation of systems helps meet the evolving regulatory requirements.
How Can Rishabh Engineering Help Integrate Automation In Plant Engineering?
We provide custom automation solutions tailored to the unique needs of plant engineering. With a proven track record of delivering excellence across various industries, Rishabh Engineering is your multi-discipline engineering company of choice that stands out for its innovative approach and commitment to client success.
- Comprehensive Automation Services: Rishabh Engineering offers a comprehensive suite of automation services, from process automation and control system integration to implementing advanced technologies such as the Industrial Internet of Things (IIoT) and machine learning. This holistic approach ensures that plant engineering is optimized for efficiency and performance.
- Customized Solutions for Diverse Industries: Understanding that different industries have unique requirements, Rishabh Engineering tailors its automation solutions to meet clients’ needs. Whether in the oil and gas sector, pharmaceuticals, or manufacturing, Rishabh Engineering’s expertise extends across diverse industries, making it a versatile partner in the journey towards automation.
- Continuous Innovation and Adaptability: In the rapidly evolving landscape of technology, Rishabh Engineering stays ahead of the curve by fostering a culture of constant innovation. Devoting resources to research and development, the company incorporates cutting-edge automation advancements, providing clients with industry-leading solutions that elevate their position in the market.
- Collaborative Approach to Client Success: Rishabh Engineering understands that successful automation implementation is not just about technology but also about collaboration. Collaborating closely with clients, the company comprehensively grasps their distinct challenges, tailoring solutions to align seamlessly with their business goals. This partnership-driven strategy cultivates enduring relationships, positioning clients for success in an era of automation.
Final Words
In the evolving landscape of plant engineering, where automation is steering transformative change, companies need partners with industry acumen and technical expertise to lead innovation. Rishabh Engineering, driven by excellence, innovation, and client success, emerges as a guiding light in automation, ushering industries into a future where efficiency, safety, and sustainability converge. Choosing automation with Rishabh Engineering is more than a decision; it’s a strategic imperative for those aiming to excel in the dynamic realm of modern plant engineering.
Seek Help With Plant Engineering Automation?
Partner with us to guide you through the essential steps of how to automate your plant operations.
Related Blogs
Related Blogs
Detailed Engineering Considerations for Project Success
Engineering projects today require meticulous planning and execution across various…
Navigating the Green Hydrogen Value Chain
Green hydrogen is a powerful contender for a more sustainable…