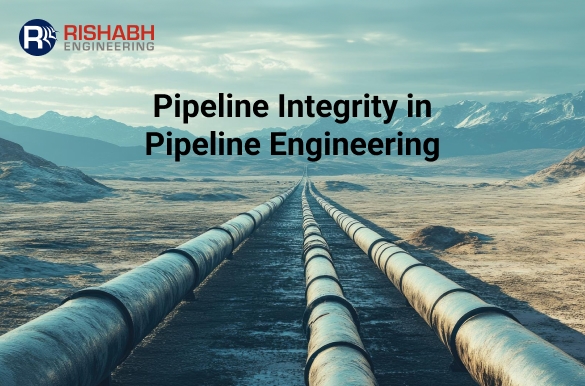
Pipeline Integrity Management For Safe & Reliable Engineering Operations
|Pipelines are an important component in transporting oil, gas, water, and chemicals across long distances—safely and efficiently. Whether it’s in the oil and gas sector, petrochemicals, or industrial manufacturing, they support operations of any scale. But just like any infrastructure, even they are subject to wear and tears, environmental stress, and operational strain. Their failures could lead to serious accidents, financial losses, environmental harm, and even human casualties. From small leaks that go undetected to catastrophic ruptures, the risks are very real. Managing the health of a dedicated system helps companies avoid these threats and ensures safe, long-term operation. And this is where pipeline integrity management becomes essential.
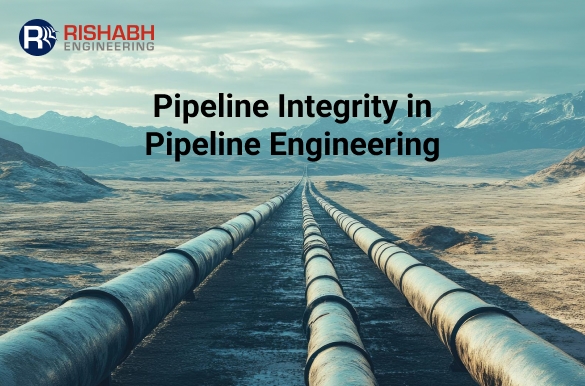
This article explores what is pipeline integrity management, its objectives, elements, challenges and best practices. We’ll also talk about how Rishabh Engineering supports companies in managing pipeline systems with care and precision.
What is Pipeline Integrity Management?
Pipeline integrity management is the methodical process of making sure that they operate as planned and without interruption. Potential dangers must be identified, pipeline conditions must be tracked, maintenance must be planned, safety rules must be followed, and essential steps must be taken before issues worsen.
This process can be broadly divided into three essential steps:
1. Assessment
Understanding the pipeline’s current state is the initial step in any integrity management procedure. This involves spotting possible dangers such as material flaws, corrosion, leaks, and damage from other parties. The objective is to collect the appropriate data to obtain a comprehensive view of its condition.
Assessment may involve:
- Reviewing past inspection reports and maintenance history
- Conducting on-site inspections using tools like smart pigs, visual checks, or pressure testing
- Evaluating operating conditions, age, and location
- Identifying high-risk sections based on their criticality to operations or proximity to populated or environmentally sensitive areas
A solid assessment enables the owners to find the foundation they need to make well-informed decisions.
2. Pipeline Integrity Planning
Once the condition is known, the next step is to develop a tailored integrity management plan. This is a living document that outlines how to maintain the pipeline’s health over time. It includes both preventive and corrective actions, scheduled inspections, and strategies for minimizing risks.
The plan typically covers:
- Risk mitigation actions (like adding protective coatings or cathodic protection)
- Inspection schedules based on threat levels and operating conditions
- Guidelines for responding to detected anomalies or potential failures
- A strategy to prioritize resources based on risk and business impact
This planning stage ensures that teams are not reacting to problems as they occur but instead working with a clear roadmap to keep its functioning optimally.
3. Project Management
Effective project management is essential when implementing an integrity management program since it necessitates collaboration between teams, vendors, and schedules. The integrity plan is executed efficiently thanks to robust project oversight, which covers everything from scheduling maintenance tasks and deploying inspection teams to recording compliance and making sure deadlines are reached.
Key project management activities include:
- Scheduling and tracking inspections and repairs
- Managing budgets and resources
- Communicating across engineering, safety, and operations teams
- Ensuring documentation is complete and meets regulatory requirements
When project management is done right, it helps prevent delays, reduces downtime, and ensures the entire integrity process delivers real results.
Objectives Of Pipeline Integrity Management
Maintaining the health is not a one-time task, it’s an ongoing responsibility. Here’s why it’s critical:
- Safety First: Pipeline failures can lead to fires, explosions, or toxic leaks. These events not only endanger workers and the public but also damage the company’s reputation.
- Operational Continuity: Downtime from unexpected issues that could affect production schedules and delivery commitments. This can result in lost revenue and customer trust.
- Environmental Protection: Leaks can contaminate soil, water bodies, and ecosystems. The cost of cleanup and legal action can be immense.
- Regulatory Compliance: Most sectors are subject to stringent safety regulations. License revocation, shutdowns, or fines could result from noncompliance.
Elements of Pipeline Integrity Management
To protect a system effectively, a comprehensive plan is necessary. Below are the main pillars of a successful pipeline integrity management program:
Risk Assessment and Analysis
Before you proceed, you need to know what could go wrong and therefore it is important to understand the system and the different risks it faces. These can include:
- Corrosion, both internal and external.
- Mechanical damage from third-party activity or natural movement.
- Stress and fatigue from pressure and temperature changes.
- Material defects or aging infrastructure.
A proper risk assessment helps you spot the most likely threats and understand how serious they could be. With that insight, you can focus your time and resources on where they’ll have the most impact. Assessing these risks helps teams prioritize which sections need more attention. Tools like risk matrices and scoring models help determine the likelihood and consequence of failure, enabling smarter decision-making.
Inspection and Monitoring
Pipelines need regular checkups, just like people do. Tools like inline inspection devices, acoustic sensors, or even drones can be used to scan for early signs of damage—cracks, corrosion, or leaks that aren’t visible from the outside. Regular inspections are essential to detect early signs of trouble. Common inspection techniques include:
- Visual inspections for surface-level damage.
- Ultrasonic testing for thickness and cracks.
- Magnetic flux leakage to identify corrosion or pitting from the inside.
- Additionally, sometimes, a pipeline shows signs of wear or damage. That doesn’t always mean it needs to be replaced. A fitness-for-service assessment looks at the extent of the problem and helps decide if the system can keep running safely with repairs, or if it’s time to take bigger steps.
These inspections generate valuable data. With continuous monitoring technologies—such as sensors and remote telemetry—companies can track conditions in real time. In some systems, monitoring tools can track pressure, temperature, and flow 24/7, helping detect unusual behavior before it becomes a major issue.
Maintenance and Repair
A strong maintenance plan includes:
- Preventive maintenance, where issues are addressed before they grow.
- Corrective maintenance, where existing issues are fixed efficiently and with minimal disruption.
- Corrosion is one of the biggest threats to system’s health. To slow it down or stop it altogether, protective coatings, cathodic protection systems, and chemical treatments are used. But the job doesn’t stop there—these methods need to be regularly checked and maintained to stay effective. If corrosion does show up, the key is catching it early and addressing it before it spreads.
- Leaks are serious—not just because they waste products, but because they can harm people and the environment. Advanced tools like fiber optic sensors, pressure monitors, and acoustic detectors can help identify leaks quickly. Once a leak is found, having a response plan in place—like isolating the section or shutting it down—can make all the difference.
Even a well-designed pipeline needs regular care. That includes cleaning, maintenance, and repairs—both planned and unplanned. Having a solid maintenance schedule in place can help extend the life of the system and reduce emergency interventions. But when something unexpected does happen, it’s important to have a clear plan for making quick, safe repairs. Proper planning ensures that maintenance doesn’t interrupt operations unnecessarily and that repairs meet engineering best practices.
Compliance and Regulatory Requirements
There are strict rules and standards that companies need to follow to make sure they are safe and properly managed. Their design is governed by national and international standards. Common regulatory frameworks include:
- API 1160 (Pipeline Integrity Management for Liquid Pipelines)
- ASME B31.8S (Gas Transmission and Distribution)
- NACE standards for corrosion control
Following these standards isn’t just about avoiding fines. Further, staying compliant means keeping good records, conducting regular audits, and making sure every step of the process aligns with the latest guidelines. It reflects a commitment to safety and operational discipline.
Challenges in Pipeline Integrity Management
Managing such systems comes with their own set of difficulties:
- Aging Infrastructure: Many of them in use today were built decades ago. Keeping them functional without full replacement requires deep technical expertise.
- Harsh Environments: They often run through remote, underwater, or desert regions—exposing them to extreme temperatures, pressure changes, or corrosion.
- Operational Complexity: Being an integrated component of the broader production systems, any repair or change must be carefully coordinated to avoid disruptions.
- Integrating Technology: While new inspection tools and sensors are available, integrating them into existing systems without downtime can be tricky.
Rishabh Engineering Team’s Experience in Pipeline Integrity Management
Rishabh Engineering has worked across the oil & gas, petrochemical, and industrial sectors to help clients improve their pipeline systems. With a team experienced in piping, mechanical, civil & structural, and instrumentation engineering, Rishabh supports the full lifecycle of system integrity—right from risk assessment to inspection planning, data evaluation, repair design, and compliance reporting.
Our designers & engineers have handled various projects involving:
- Pipeline stress analysis using tools like CAESAR II.
- Detailed engineering to upgrade sections for better performance.
- Integration of inspection data with models to forecast degradation.
- Reports and recommendations aligned with API, ASME, and NACE codes.
Whether it’s a small process line in a manufacturing unit or a cross-country transmission system, Rishabh’s team brings deep technical know-how and an organized approach to system management.
Pipeline Integrity Management Best Practices from Rishabh Engineering’s Perspective
Drawing from years of project experience, Rishabh Engineering recommends the following practices to ensure they remain reliable and safe:
- Develop a Comprehensive Integrity Management Plan: This should be a living document outlining inspection schedules, risk prioritization, data management strategies, and contingency plans.
- Conduct Risk Assessments Regularly: Instead of a one-time review, assessments should be made periodically or whenever operating conditions change.
- Implement Predictive Maintenance: Relying solely on reactive maintenance leads to higher costs. Predictive approaches help address problems early, reducing downtime and expenses.
- Train Personnel: Training operations staff to recognize warning signs and interpret monitoring data is just as important as the tools themselves.
- Use Cross-Disciplinary Expertise: From material engineers to stress analysts, bring in the right specialists for different tasks to cover all technical angles.
Final Words
Since pipelines are the foundation of industrial and energy infrastructure, their dependability cannot be disregarded. A robust integrity management program and efficient pipeline engineering services are necessary to protect people, the environment, and business operations. From routine data analysis and inspections to timely repairs and regulatory compliance, every part contributes to preserving their operational fitness, safety, and efficacy. Businesses are better prepared to handle the operational problems of today and the demands of tomorrow when they adopt a proactive, organized approach to integrity management. Our expertise in design, risk assessment, compliance support, and maintenance planning ensure that your infrastructure remains reliable and strong whether you’re building new systems or extending the life of existing assets. Together, we can maintain the security and optimal functionality for the piping infrastructure.
Looking To Safeguard Your Pipeline Operations?
Rishabh Engineering team can help maintain pipeline health through risk assessment, inspections, repairs & regulatory compliance.
Related Blogs
Related Blogs
Underground Pipeline Stress Analysis for Effective Design
In this article we will discuss the importance of underground…
Cross Country Pipeline Design & Engineering
Cross-country pipelines help transfer natural resources such as oil and…