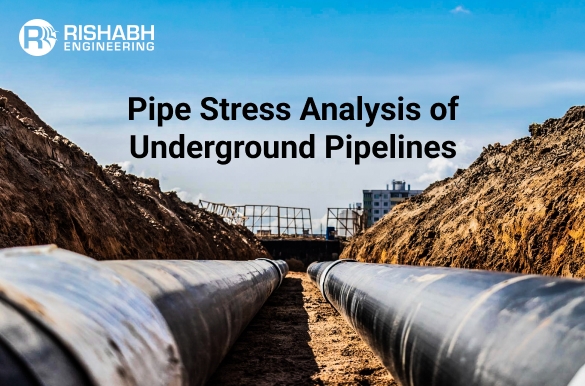
Underground Pipeline Stress Analysis for Effective Design
|Underground pipelines are essential for transporting a wide range of materials, including oil, gas, water, and chemicals, over long distances. Their design, installation, and maintenance require comprehensive engineering and risk management to ensure safety, efficiency, and longevity. One of the most crucial aspects of pipeline design is pipe stress analysis, which evaluates the structural integrity of pipes under different operational conditions, including temperature variations, pressure changes, and external forces.
In this article we will discuss the importance of underground pipeline stress analysis, its methodologies, key considerations, and the role of multidisciplinary engineering in ensuring the robustness of pipeline systems.
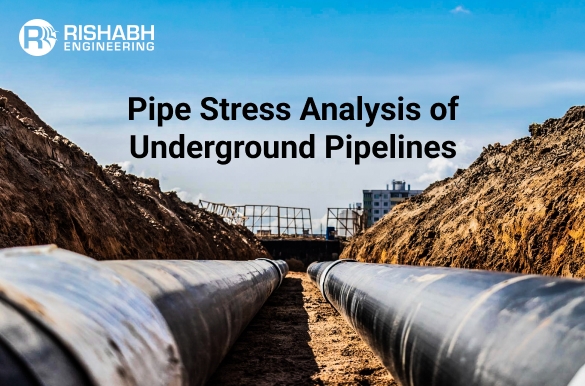
The Role of Underground Pipeline Stress Analysis
Pipe stress analysis is a critical engineering process used to assess how external forces and internal pressure impact a pipeline’s structural performance. This analysis evaluates the ability of the pipe to withstand mechanical stress without failure, which is especially important for underground systems where external forces—such as soil movement, traffic loads, and environmental conditions—can significantly impact the pipeline’s integrity.
It helps ensure the following:
- Structural Safety: Preventing failure due to excessive stress, which can lead to pipeline rupture, leaks, or collapse.
- Compliance with Standards: Ensuring adherence to industry standards, such as the ASME B31.3 (for Process Piping) and ASME B31.4 (for Liquid Transportation Systems), ASME B31.8 (Gas Pipelines) which outline the design, construction, and operational limits of pipelines.
- Operational Efficiency: Identifying design improvements to reduce wear and tear, mitigate risks, and optimize the system for long-term performance.
- Risk Mitigation: Proactively identifying points of vulnerability, including pipe bends, tees, and junctions, where stress is concentrated.
Characteristics of Underground/Buried Pipelines
- High Allowable Stress: A pipe has a circular shape and often runs several miles before turning. Hence, the calculation of stress is through simple static equilibrium formulas, considered as the most reliable ones. As the produced stresses are predictable, the permissible stress for the plant piping is considerably higher.
- High Yield Strength Pipe: The first obstacle is to raise the allowable yield strength. Although the pipeline that operates above the yield strength does not create the problems of structural integrity, it can cause undesirable deformation and chances of strain follow up. Therefore, for the construction of pipelines, a high test line with the very high ratio of yield to ultimate strength is used. All the allowable stresses have yield strength as the only basis.
- High-pressure Elongation: The movement of a pipeline is generally because a very long line’s expansion has a low-temperature difference. The pressure elongation is negligible in a plant piping, contributing much to the total movement and hence should comprise the pipe stress analysis.
- Soil-pipe Interaction: As a huge part of a pipeline is buried underground, any movement in the pipe has to overcome the soil force, generally divided into two categories: (i) Friction Force Created by Sliding, and (ii) Pressure Force Resulting from Pushing. The most crucial task of underground pipe stress analysis is to investigate the soil-pipe interaction, which does not matter in the plant piping analysis.
Importance of Multidisciplinary Engineering in Pipeline Stress Analysis
Pipe stress analysis for underground pipelines is not a standalone process—it involves collaboration across various engineering disciplines, including mechanical, civil, structural, and geotechnical engineering. A multidisciplinary design engineering company, like Rishabh Engineering, plays a crucial role in ensuring that all aspects of the pipeline system are accounted for, from soil analysis and material selection to stress mitigation and installation.
A multidisciplinary approach ensures that:
- Design Optimization: Engineers from various disciplines collaborate to create the most efficient and cost-effective design.
- Risk Identification: The team can identify potential risks from multiple perspectives, reducing the likelihood of unforeseen failures.
- Holistic Solutions: By integrating various engineering disciplines, Rishabh Engineering provides comprehensive solutions that address both technical and practical challenges in underground pipeline design and installation.
Explore this blog to learn the major factors of cross-country pipeline design & engineering by multidisciplinary engineering firms, highlighting the critical phases and activities involved in complex projects.
Methodology Of Conducting Underground Piping Stress Analysis
Underground pipe stress analysis is conducted using specialized software tools like CAESAR II and STAAD.Pro to simulate various conditions that affect the pipeline. They consider factors like temperature fluctuations, pressure cycling, pipe material properties, installation conditions, and external loading. However, piping flexibility analysis, as well as the stress analysis for the underground piping system, is carried out using CAESAR II software. It provides adequate flexibility to absorb thermal expansion, displacement incurred in the buried piping system, and code compliance for stresses.
The buried piping stress analysis is broken down into several key steps:
- Modeling the Pipeline: It involves creating a detailed 3D model of the pipeline, including all relevant components such as elbows, valves, flanges, supports, and bends. It serves as the basis for further analysis.
- Defining Boundary Conditions: The analysis software helps apply boundary conditions such as temperature, pressure, and external loads (e.g., soil weight, vehicular traffic) to simulate real-world conditions. Temperature variations, especially for buried pipelines, can cause significant expansion or contraction, affecting the pipeline’s stress.
- Applying Load Cases: Different load cases are considered, including operational loads (internal pressure, temperature changes), external loads (soil movement, seismic forces), and accidental loads (blowouts, impacts). Each case is analyzed to determine how it affects the pipeline at critical points.
- Evaluating Stress and Strain: The software calculates the induced stress and strain in each section of the pipeline. The primary focus is on determining whether the pipeline can handle the expected stresses without exceeding the allowable limits for the pipe material.
- Identifying Critical Areas: The analysis identifies locations where the stress is highest, such as near bends, welds, or junctions. These critical areas are then assessed for potential failure points and required modifications, such as increasing the pipe thickness, adding additional support, or changing the material used.
- Final Report and Recommendations: After running the analysis, engineers generate a comprehensive report that includes recommendations for mitigating stress-related risks. This may involve design changes, material upgrades, or the introduction of additional protective measures.
Key Considerations in Buried Pipeline Stress Analysis
There are several factors that engineers need to consider when performing pipe stress analysis for underground pipelines. These include:
- Soil-Related Forces: The condition of the soil surrounding a buried pipeline has a direct impact on the stress levels experienced by the pipe. Soil settlement (caused by moisture changes, ground shifting, or natural subsidence) can lead to additional external loads, while frost heave and earthquake forces can create severe stresses on buried pipelines. Engineers must account for the type of soil and its behavior under varying conditions.
- Temperature Variations: Underground pipelines are subject to temperature fluctuations both at the surface level and within the surrounding environment. These fluctuations can cause the pipeline to expand or contract, resulting in thermal stress. Engineers must consider the temperature variations over the course of the year and the potential for extreme weather conditions.
- Pipe Material and Diameter: The material properties of the pipe—such as its yield strength, elastic modulus, and coefficient of thermal expansion—affect its ability to withstand stress. Additionally, the pipe’s diameter and wall thickness must be sufficient to handle internal pressure and external forces.
- Pipe Supports and Restraints: Properly designed pipe supports and restraints are essential for distributing external loads and preventing excessive bending and sagging. The spacing and placement of support are crucial factors that can influence the overall stress levels in the pipeline.
- Dynamic Loads and External Events: External loads, such as traffic loads from vehicles passing over the pipeline or seismic forces, can introduce dynamic stresses that affect the pipeline’s integrity. In earthquake-prone regions, seismic analysis is particularly important to ensure that the pipeline can handle ground movements without failure.
- Pipeline Configuration: The configuration of the pipeline—whether it involves long, straight sections, curves, or intersections with other pipelines or structures—can influence the stress distribution. Sharp bends or sudden changes in direction create localized stress concentrations, which may require additional reinforcement.
How Can Rishabh Engineering Support with Underground Piping Stress Analysis?
We ensure structural integrity and adherence to industry requirements by offering thorough pipe stress analysis for subterranean pipelines. Utilizing sophisticated software such as CAESAR II, the team performs comprehensive evaluations to examine external forces, pressure variations, and thermal expansion that may impact the pipeline’s functionality. Bends, junctions, and submerged portions are examples of areas of concern and possible stress sites that could be susceptible to failure, and this piping stress analysis helps identify them. To reduce hazards, Rishabh’s multidisciplinary approach combines skills in structural, mechanical, and civil engineering to provide optimal design solutions.
Real Life Case Study
Case Study: Underground Pipeline Stress Analysis for Lean Gas Pipeline Project
To illustrate the importance of pipe stress analysis in practice, consider the example of a lean gas pipeline detailed engineering project undertaken by Rishabh Engineering. The project, which involved a 2-week engagement for a client based in North America, focused on performing pipe stress analysis for 15 critical pipeline segments within an Air Treatment Module.
Project Deliverables
The buried pipeline stress analysis project involved the following key deliverables:
- Stress Analysis for 15 Critical Lines: The goal was to evaluate the pipeline’s ability to withstand mechanical stress due to temperature fluctuations, internal pressure, and external forces.
- Recommendations for Stress Mitigation: Based on the analysis, recommendations were made to modify pipe supports and adjust pipe thickness to meet code requirements.
- Displacement Data for Tie-In Points: Accurate tie-in point displacements were calculated to optimize the installation process and minimize stress-induced risks during the operational phase.
Scope of Work
The scope included performing detailed stress analysis for critical pipeline sections within an air treatment module, using CAESAR II for modeling and analysis. The primary focus was on complying with ASME B31.3 (Process Piping) standards and ensuring that the design could handle thermal and mechanical stresses, while also optimizing performance and reducing risks.
Rishabh Engineering Solution
To address the challenges of the pipeline stress analysis, Rishabh Engineering implemented the following solutions:
- Customized Stress Modeling: Using advanced simulation tools, Rishabh’s engineers modeled each pipeline section to account for internal and external pressures, thermal expansion, and soil-related forces.
- Code Compliance: The design was aligned with ASME B31.3 code requirements, ensuring that the system would meet industry safety and performance standards.
- Stress Mitigation Strategies: Based on the analysis results, Rishabh provided design modifications, such as adjusting pipe support configurations and recommending specific materials for high-stress areas.
Final Words
An essential part of pipeline engineering services, underground pipeline stress analysis guarantees the performance, longevity, and safety of pipeline systems. Engineers can make well-informed design and material decisions by assessing stresses resulting from internal pressure, thermal expansion, and external forces. Optimal design and complete adherence to safety regulations were made possible by the lean gas pipeline project’s efficient stress analysis. Businesses such as Rishabh Engineering utilize multidisciplinary teams to address difficult problems and provide trustworthy answers. Whether for aboveground or subterranean systems, careful stress analysis is essential. By collaborating with seasoned engineers, all risks are taken care of, producing strong pipes that last.
Seek Help With Pipeline Stress Analysis?
Our multidisciplinary specialists can help you ensure safety, compliance, and performance in your underground systems.
Related Blogs
Related Blogs
Cross Country Pipeline Design & Engineering
Cross-country pipelines help transfer natural resources such as oil and…
Importance Of Multidisciplinary Approach To Pipeline Projects
For the long-distance transportation of vital commodities like water, gas,…